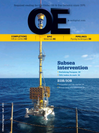
Page 56: of Offshore Engineer Magazine (Apr/May 2015)
Read this page in Pdf, Flash or Html5 edition of Apr/May 2015 Offshore Engineer Magazine
Pipelines
In? atable
Chris Sparrow shows how using in? atable buoyancy for pipelaying support operations could result in shallow-water savings. he “time is money” equation may well be the most
T overused business cliché, but it is still as true and as relevant to pipeline installation in 2015 as it ever has been.
For pipeline installation contrac- tors, the primary consideration is to get the job done and to be offsite and onto the next project as safely, as ef? ciently and as quickly as possible.
Buoyancy used on such opera- tions is very often viewed as a nec-
In? atable buoyancy units during deployment on evil, and maybe not given as essary
Wheatstone. Photo from Allseas.
much consideration as it could be, knock-on effects of using an inef? cient While steel is still being used by some, the as the buoyancy solution are often hidden – although market is moving towards safer and more ef? - they can have a major impact on the overall cient technologies.
costs of a project.
Contractors have the ability to fabricate their The plastic revolution
Over the past 25 years, a number of manu- own steel buoyancy tanks and may, therefore, facturers have emerged offering two types of look no further than that when looking to ? oat or plastic buoyancy for installation projects: solid pull a pipeline into position. However, the poten- (i.e. foam-? lled) and in? atable. tial savings to be made using buoyancy solutions,
Solid plastic buoyancy is now in widespread which create greater ef? ciencies as well as a use. It is typically formulated from syntactic reduction in the risk pro? le can be enormous. foams for deepwater applications, but it is also
The past sometimes seen in use at, or near, the surface
Historically, contractors needing buoyancy on pipeline installations. While there may be for a pipelaying operations would probably some relatively minor variation at depth and have welded up some old oil drums and then over time in the total amount of buoyancy abandoned them at the end of the project. More that such units can offer, they will generally recently, in-house fabricated, enclosed steel provide near-constant amounts of buoyancy cylinders became the norm. The drawbacks to throughout their service lives. This is perfect using steel include: in scenarios such as riser buoyancy, where a • It is heavy, large, hard to transport, handle and constant amount of uplift is required at depth.
deploy, requiring specialized lifting equipment. However, solid buoyancy has disadvantages •
It needs to be outsize to support its own in shallow water applications. Although lighter weight, before offering extra buoyancy to lift than steel units, solid plastic units are heavier loads—a particular drawback in shallow-water than in? atable units and, as with steel units, works where every foot of un-necessary pro? le they will also require special lifting equipment requires an extra foot of trenching to deploy. Also, as with steel, the extra weight •
Units become a projectile, when released will result in a bigger unit with a bigger pro? le from the submerged pipeline at the end of the to produce the same amount of uplift as a much process. smaller in? atable unit.
•
Units deteriorate between projects resulting If, as a contractor, you are looking to remove in ongoing maintenance requirements. 85% of the weight of a 28in pipeline to bottom pull it through <1.5m of water, it is likely that solid plastic units will sit too high in the water
IBUs on Tie-in panoramic. Photo from Allseas.
April 2015 | OE oedigital.com 58 058_OE0415_Pipelines2_Unique.indd 58 3/23/15 6:29 PM