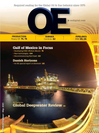
Page 98: of Offshore Engineer Magazine (May/Jun 2015)
Read this page in Pdf, Flash or Html5 edition of May/Jun 2015 Offshore Engineer Magazine
pipes prior to welding and measurement operators were laying in trenches, thus required per shift until all the preventing environmentally pipe pro? le measurement data damaging leaks. In parallel, had been collected (after which
OMS has developed bespoke they were demobilized).
Pipelines laser measuring equipment OMS numbered the pipes in and methodologies with sup- the pipe stack (prior to beveling) porting software, for optimiz- to sequence the pipes ready for ing pipe ? t-up. The service the riggers to collect. No extra reduces costs for customers pipe handling was required through faster pipelaying and here, as only planned pipes were improves quality by eliminat- moved. Rotation marks were then ing misaligned pipe ends. applied to the pipes once they
Each pipe end is measured, were placed on the ready rack.
Pipes being unloaded from a supply barge to the pipelaying identi? ed and entered into the Using pipe optimization vessel.
pipe optimization software, software, it was found that most which analyses the ? t-up of of the pipe joints would fail pipes and allows the opera- the acceptable HiLo criteria in tor to mark the best rotational multiple positions. However, position on each pipe end. the project HiLo could be
In the bead stall, these marks achieved at certain positions are aligned to immediately when the pipes were rotated. In achieve the best rotational the following example, possible position so that misalignment misalignment was 0.4mm at best is minimized and the project rotation, but up to 1.3mm at
HiLo is easily achieved. worst. Result: 300% increase in
Any problem pipes that weld rate.
won’t ? t at a speci? ed HiLo All pipe joints sent through are also indicated and can to the bead stall were within the be re-sequenced or removed client requirement of 1mm HiLo. completely so that ? t-up prob- The weld rate was increased to The SmartFit software has the ability to sequence single and lems do not occur in the bead an average of 40-45 welds per multiple pipe ends (i.e. doubles, triples and quads).
stall. Production delays due to day — an increase from the ini- misaligned pipes are avoided. Project details tial rate (i.e. 15 welds per day) of 300%.
• Pipe size: 16in nominal/406.4mm x 21mm
Experience shows that with typical In addition, OMS was able to assist + 3mm CRA (corrosion resistant alloy) ? owline HiLo limits — and using typi- with traceability issues, including iden- • cal seamless line pipe that has not been Quantity: Approximately 1100 pipes tifying any pipe numbering duplicates • counter-bored — ? t-up issues can occur HiLo permitted: 1.0mm internal or errors. OMS not only helped speed regularly. For a HiLo of around 1.0mm maximum up the welding process through the time • to 1.2mm, problems are likely to occur Long seam weld control: Top 90°, sepa- saved in lining up the pipes, but also every 10 to 20 pipes (this varies accord- ration of 100mm (minimum) helped to reduce the number of weld ing to the exact type of pipe). Using The customer had already carried out repairs and cut-outs. pipe optimization software enables the end dimensioning of the pipes prior to required HiLo’s to be achieved in the OMS’ involvement. After measurements Since joining OMS in bead stall without trial and error. It also were taken, the customer deemed the 2006, Denise Smiles identi? es problem pipes in advance, so pipes to be satisfactory and within the has been actively that this can be removed from the pipe manufacturing speci? cation. Welding of involved in the welding sequence, therefore avoiding any the pipes began offshore on the pipelay- execution of many problems in the bead stall. ing vessel, with a target of 40 welds per deepwater oil and
Elements of pipe optimization can day. Unfortunately, this target was not gas projects that be deployed in various ways to suit the achieved due to poor pipe ? t-up leading required improve- practicalities of different production pro- to excess HiLo. The peak weld rate at that ment of dimensional tolerances, ? t-up cesses, both onshore and offshore. OMS time was approximately 15 welds per day. solutions in the ? ring line and delivery of has applied the system aboard a wide OMS deployed a team of three opera- speci? c pipeline architectures to ensure variety of pipelaying vessels and spool tors direct to the pipelaying vessel. This best ? t-up with dif? cult pipes, including bases around the world. meant that there was no opportunity Gorgon (Chevron), Quad 204 (BP), for upfront analysis of pipe measure- Wheatstone (Chevron), Ichthys (Inpex),
Case Study: O