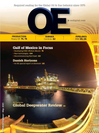
Page 60: of Offshore Engineer Magazine (May/Jun 2015)
Read this page in Pdf, Flash or Html5 edition of May/Jun 2015 Offshore Engineer Magazine
Images from ZerLux Hungary Ltd.
Concept Images
Page 1: Fine-tuning laser shots at ZerLux
Page 2: Fiber optics at work
Page 3: Hard scale Removal Test
Page 4: Panel design.
Page 5: The Core Laser Team
IMG 7158: Engineers work on perforation tool
DSC00491: Laser Drilled Sandstone Core Sample
Laser drilled sandstone core sample.
Images from ZerLux Hungary Ltd.
Drilling
Laser-like
Engineers work on perforation tool
Yet, despite these advances, govern- precision ment funding for laser drilling research at institutions such as Argonne National array of mechanical components associ- Laboratory (ANL) has been cut. In
Jerry Lee and Greg App ated with traditional drilling operations, response to this lack of government sup- examine how lasers could the time associated with tripping in and port, various private organizations have out and replacing or repairing compo- built upon the progress already made. be used for not just drilling, nents. Effciency is realized due to the For example, Foro Energy, the company but for completions and well continuity of the laser drilling operation. responsible for the development of the intervention projects, too.
Once the operation begins, there is no bit SBS fber optics, was formed by members to replace, and thus less cause to trip in of the original laser drilling research he oil and gas sector is con- and out. A laser drill can remain opera- partnership between the Colorado School stantly seeking innovations to tional as long as there is an available of the Mines and ANL.
T improve economic effciency, power source. Initially, two methodologies were particularly to decrease the high costs Further progress toward commercial- considered for the laser drilling drive associated with drill bits and non-pro- izing laser technology was spurred by mechanism: rock melting or the spall- ductive time (NPT). This need for con- the automotive industry. This investment ation of the grains. Spallation occurs tinuous improvement helped spark the resulted in the cost of 1W of laser drill- when laser-induced thermal stresses are frst phase of the Gas Research Institute ing power dropping from US$1000/W to applied to the grain causing it to fracture; (GRI) funded research program aimed at less than $50/W. Another major obstacle however, the amount of energy applied utilizing high-powered lasers for drilling. cleared was to prove that laser drills are by the laser must be low enough to keep
Following the release of previously clas- not limited by the type of lithology. the local temperature below the melting sifed information from the US Defense There were also problems with the use temperature. Depending on irradiance,
Department’s Star Wars Laser technology of fber optic cables due to Stimulated or power per unit area, the laser rock in the mid-1990s, some in the oil and gas Brillouin Scattering (SBS). “[SBS] chokes interaction can cause the grains to melt industry have developed an interest in off the transmission of high power laser or spallate. harnessing the potential of laser drilling. photons in a fber optic cable by refect- “The most effcient way to laser drill
The primary advantage of utilizing ing the energy backwards to catastrophi- through sandstone is spallation, where lasers lies in cost effciency. In traditional cally destroy both the fber optic cable laser energy is used to break the bonds drilling operations, progress is often and laser source,” says Foro Energy. holding the grains together, creating loose halted by the replacement of worn-out However, with the introduction of SBS sand particles,” says Neal Skinner, senior bits, stuck pipe and other inevitable resistant fber optics, the issue has been scientifc advisor at Halliburton. The malfunctions. Halting operations results resolved. Additionally, current laser drill- grains are then removed to expose the in lost time and money. Another key ing developments have seen power avail- next layer of rock. method of reducing expenditure is the ability increase from 1kW to 1000kW, as “Shales also spall in a manner similar reduction of rig rental time. NPT is sig- well as improvements in unit mobility to sandstone. Limestone, however, is nifcantly reduced by removing the vast and durability. mainly calcium carbonate and undergoes
May 2015 | OE oedigital.com 62 062_OE0515_DC3_Lasers.indd 62 4/20/15 8:13 PM