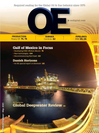
Page 62: of Offshore Engineer Magazine (May/Jun 2015)
Read this page in Pdf, Flash or Html5 edition of May/Jun 2015 Offshore Engineer Magazine
Drilling
Hard scale removal test. Fiber optics at work.
done underbalanced, utilizing water and laser power needs to be delivered down- a different process for laser removal,” he the bottomhole assembly. Additionally, nitrogen instead of drilling mud. hole,” Halliburton’s Skinner says. explains, adding that under temperature, the system’s electronics are susceptible to
The use of laser systems in comple- limestone dissociates into calcium oxide heat damage when external temperatures
Advantages of laser completions tions operations is feasible because and carbon dioxide [CaCO -> CaO + rise above 200°C.
3
CO ]. “Calcium oxide is a white powder such systems can be incorporated with Perforation techniques used to complete 2
Ofshore applications and easily purged from the hole with gas existing equipment. “The tool will be conventional wells often cause exten- sive formation damage. However, laser mounted on coiled tubing, which will sit or liquid.” Laser technology is not confned solely perforation causes no formation dam- on top of a specially customized bottom- to perforations or drilling applications. It
Contemporary application age, and will extend past the formation hole-assembly,” Bajcsi explains. “The also has potential as a well intervention damage caused by the drilling process, idea is that we deploy the high-power The technology and the benefts sur- tool. The mediation of barium sulfate thus resulting in good pay zone-well laser source from the surface and transfer rounding laser drilling are enticing. hardscale accumulation in offshore wells communication. the laser light through optical cables to However, economics are usually the is often challenging due to its resilience “It is believed that the high tempera- the laser head, which is going to drill governing factor when making decisions to most conventional well intervention ture gradients generated in nearby rock into the formation reaching into the pay in the oil and gas industry. Currently, techniques. creates stress, which causes microscopic zones,” The laser generator on the sur- implementing laser drilling technology “Laser light will change the physi- fssures or cracks to form, increasing face provides a steady stream of energy is not as cost effective as conventional cal and chemical properties of the scale permeability,” Skinner says. Due to the through the fber optic cable transferring drilling. and that will allow very fast removal,” positive correlation between payzone- 60-100kW of energy, equivalent to more “The issue is economics,” says Dr. Bajcsi says. “No other technology can well communication and production than 1000 streetlights. Peter Bajcsi, COO at ZerLux. “It sim- do that. Conventional milling just won’t output, overall production is improved. The focused beam melts the grains ply makes no business sense to deploy work.” The accumulation of hydrates in
Additionally, laser perforation results and creates molten rock, which cov- lasers to drill big vertical boreholes. fowlines and other subsea components in lower water coning, reduced sand ers the borehole with a glassy layer Conventional drilling is still more eco- is another common problem affecting incursion, and more precision and con- of obsidian, fusing the borehole and nomical to drill long laterals because the offshore operations. Hydrate forma- trol than conventional technology already exists. tion reduces production rates and can perforation. Hydraulic Conventionally drilled lat- completely plug a piece of equipment. fracturing can similarly erals improve the produc- To address this issue, ZerLux developed beneft from the utiliza- tivity of the wells and even two technologies — Blue Tube and Intra- tion of laser technology connect two pay zones, so Snake — to facilitate hydrate mediation. by creating small starting that’s not what we’re after.” The tools use a conventional remotely holes for the fracturing With the associated operated vehicle to scan equipment and process. equipment, supplies, and selectively heat the affected area with its “Small-scale rock- services being readily laser to treat the blockage without physi- mechanics laboratory available, drill jobs can be cal contact. This capability also allows tests suggest that if it undertaken less expensively hydrate plugs of varying length to be were possible to make by conventional methods. addressed, not just small plugs. “These two technologies will allow
The industrial logistics a 1-2ft-long perforation
The Core Laser Team operators to remove hydrates without necessary for industry-wide perpendicular to the well- entering the pipe. It is safer and much laser drilling applications do not yet increasing borehole stability. This bore, it would allow a bypass from the more economical than electric blan- exist. Due to this limitation, the cur- naturally impermeable glassy layer is [damaged zone] to create more linear, less kets and other conventional methods,” rent focus of laser technology is on well made permeable by ZerLux’s proprietary tortuous fractures,” he says.
Bajcsi says. completions. methodology resulting in improved Though industry has seen maximum perforation depths of around 4ft, ZerLux communication between the reservoir “Laser perforating has its own value Although lasers cannot economically is building a tool that could penetrate and the wellbore, as well as resisting proposition and is easier than laser address all the technology challenges, the reservoir to 10-20ft deep while sand incursion. The specially designed drilling. A certain irradiance or optical laser technology has the potential maintaining a larger diameter than that laser head then fushes out the debris, power per unit area must be delivered at to improve effciency in the oil and created by a perforation gun. However, which is composed of thin, brittle the rock face to make things work. With gas industry, as well as open up new its limits are dependent on the length of fberglass. The completions operation is a smaller hole, there is less area so less opportunities.
May 2015 | OE oedigital.com 64 062_OE0515_DC3_Lasers.indd 64 4/20/15 8:14 PM