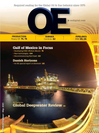
Page 72: of Offshore Engineer Magazine (May/Jun 2015)
Read this page in Pdf, Flash or Html5 edition of May/Jun 2015 Offshore Engineer Magazine
breakdown deposits would degrade and/ technology, to name a few. However, effectively on topsides and may have or clog the system, by creating further there is no confdent way to look at the application for the subsea, too. Likewise secondary localized corrosion cells. status of subsea infrastructure. Most various probes, which are designed to
However, it is an option that is still being of the inspection is conducted visu- withstand high pressure and high tem-
EPIC considered and coating companies are ally, either subsea via ROV or from the peratures, can be used to measure near reformulating products for high-tempera- instantaneous metal loss (i.e. ER, LPR, ture and high-pressure environments. potential probes). Similarly, U/T map-
Of course, in principle the major ping and guided wave technologies are “Pipeline failure beneft of using CRAs is that operators gaining ground in terms of application. don’t need to use chemicals or inhibitors. Through calibration and qualifcation is attributed to
For steel alone, it is always required to with blind controls and artifcial defects internal corrosion have an acceptable inhibitor effciency is always recommended by indepen- (typically 90-97%), and an acceptable dent third-party to verify reliability and about 50% of the time” availability (often 90-98%) for the steel/ accuracy. The growth of these and other inhibitor combination to work. Prolonged methods all have a way of better making
Binder Singh, Principal Integrity periods without an inhibitor can pose a the case for integrated or total integrity
Engineer, Genesis Oil and Gas.
problem if new corrosion initiation cells management programs. Most, if not all, are created or old ones are re-activated. such plans ultimately save money and
A well-selected and applied CRA, by offer a good ROI, but it’s the improve- comparison, simply does not require that topsides of the platform, where access ment on existing methods and tools type of maintenance. is better. Often a change in monitoring which are likely to provide the differ- technique depends on the data and trend entiators to capture and monetize safety
Ongoing management assessment. That’s where intelligent (or and integrity management.
Ongoing monitoring after installation smart) pigging comes into play. Pigging
Overall, the subsea environment is diffcult. As noted earlier, failure can plays an important role to check for the captures and records full length informa- corrosion condition of a pipe or a riser. tion for future trend analysis and risk- also happen on the exterior of the pipe, but the biggest concern may be at the
There are different assessment methods: based inspection planning. probe, coupon, monitoring spool pigging, Coupons, which calculate the mate- touch down zone of the steel catenary riser interface, as it connects to the advanced mapping and guided wave rial loss more directly, can also be used 072_OE0515_EPIC4-Genesis.indd 74 4/20/15 4:01 PM