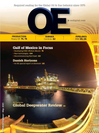
Page 96: of Offshore Engineer Magazine (May/Jun 2015)
Read this page in Pdf, Flash or Html5 edition of May/Jun 2015 Offshore Engineer Magazine
Pipelines
End dimensioning of pipe ends at an onshore pipe coating yard.
Images from OMS.
Ensuring the integrity of fatigue-sensitive SCRs sometimes has to take place on
Denise Smiles, of Optical a cargo barge. This measure-
Metrology Services Ltd (OMS) , ment data, if used correctly, can then help to ensure that discusses how to correct pipes delivered into the bead internal HiLo misalignment stall will ? t together easily and between butted pipes.
within the welding speci? ca- tion requirements. Better weld
Internal HiLo misalignment between butted pipes.
eepwater oil and gas pipeline quality will lead to fewer cut projects present many chal- outs and repairs, reducing costs
D lenges. As deepwater oil ? eld for the pipeline contractor.
developments increase around the world, The measurement tools can ? xed facilities are not always a viable be used to measure the inner option. Floating production systems are diameter (ID), outer diameter therefore increasing in number, which (OD) and wall thickness (WT) require unsupported riser designs. of pipe ends in rapid time.
However, these unsupported risers are
Typically, several thousand subject to signi? cant loads from ocean
ID and OD measurements of tides, storms, currents and swells, creating a pipe end can be measured a highly dynamic environment for the steel simultaneously in less than 10 catenary riser (SCR). This, in turn, necessi- seconds, enabling hundreds tates design and fabrication processes that of pipe ends to be measured
OMS’ automatic pipe end dimensioning tool.
mitigate stress and fatigue factors. Ensuring in one shift. In some circum- the integrity of fatigue-sensitive SCRs
One method of dealing with HiLo stances, pipe ends can be measured in is therefore one of the most challenging misalignment is to counterbore the pipes, stacks. This means less time on site and aspects of deepwater development.
but this might not be a viable method of less pipe handling (reducing costs), thus
A number of highly critical aspects controlling pipe geometry due to cost minimizing delays and costs for the of the pipe fabrication process must be considerations or to limitations on pipe pipelay contractor. Laser measurement guaranteed to be correct. One of these is wall thickness. If counterboring is not tools are also very accurate (typically to the internal HiLo misalignment between viable, how can a pipeline contractor 0.05mm).
butted pipes. ensure that the pipe ? t-up, welding and Data from laser measurement tools can
Minimization of HiLo contributes to pipelaying processes run smoothly with be made available to pipe optimization a good weld and decreases stress at the minimal interruption? software, which will include some sort weld joint. Typically the HiLo is required To help prevent these kinds of of simulation or sequencing software. to be less than 0.5mm in fatigue-sensitive bottlenecks, save costly delays and to SmartFit, the winner of a Queens Award pipeline sections. In engineering terms, minimize project risk, pipe end geometry for Innovation in 2014, is a system this is a considerable challenge, particu- can be captured, recorded and analyzed. developed by OMS for managing pipe larly given that the pipe used in these Automatic, laser-based measurement preparation and ? t-up in readiness for applications is often seamless, which tools can be used to measure geometrical welding prior to pipelaying. Used pre- means it inherently has wall shape and features of pipe ends, normally per- dominantly in the oil and gas industry, thickness deviations. formed onshore, although this process this system ensures accurate ? t-up of
May 2015 | OE oedigital.com 98 098_OE0515_Piplines3_OMS.indd 98 4/20/15 9:14 PM