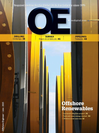
Page 39: of Offshore Engineer Magazine (Jun/Jul 2015)
Read this page in Pdf, Flash or Html5 edition of Jun/Jul 2015 Offshore Engineer Magazine
by a vacuum-testing program during the Fatigue life reassessments to continu- Based on a paper presented at the •
EPIC frst two years of operation. ously compare operational parameters to 2015 Offshore Technology Conference in
Also, to reduce the probability that design parameters. Houston, Texas.
Together, BP and Wood Group Kenny embedded debris can occur in the designed a robust and ft-for service riser
I-tube, the Q204 risers will include a
FURTHER READING system, capable of operating in one of the second protective outer sheath than most severe environmental conditions in will be thicker than the external sheath.
Project directors from BP the world. The design is based on lessons
Furthermore, a layer of Kevlar tape and Wood Group Kenny learned from a history of operating experi- will be wrapped between the two outer detailed BP’s Quad 204 ence in the offshore West Shetland a region. sheaths to bolster the impact resistance subsea redevelopment for
The fnal riser system will be a combination of the outer protective layers. The design
OE in July 2013.
of state-of-the-art bespoke hardware and includes access hatches below the riser www.oedigital.com/component/k2/ integrity-management tools for the harsh hang-off location so cameras can be item/3480-quad-204-takes-shape-subsea weather foating production system. inserted as needed into each I-tube to inspect the risers.
As if the harsh weather and strong cur- rent weren’t enough, the designers had to plan for damage from marine life as well.
In this location, buoyancy modules are vulnerable to hard marine growth such as cold-water coral. If left unchecked, the heavy buildup of coral causes integrity concerns due to the signifcant loss of buoyancy. To avoid this hazard, the designers of Q204 incorporated specif- cations for a ft-for-purpose anti-fouling layer to be applied to the buoyancy modules that is expected to retard hard- coral growth attachments. As a result, the
Q204 will have the only red buoyancy modules in the North Sea.
Integrity management
The Q204 integrity management system will be a risk-based system that relies on the probability of damage or failure as doc- umented by known fexible pipe failure modes described in the public domain, as opposed to company experience, because
BP has never experienced a fexible pipe failure. The integrity management proto- col that pertains to fexible risers, bend stiffeners, buoyancy modules, hold-down and hold-back arrangements and cathode protection systems will include: •
I-tube camera inspections of bend stiff- eners and borescope inspection of risers inside the I-tubes •
Real-time monitoring of the chain-table geometry for early detection of bend stiffener damage •
Annual-vacuum testing to confrm the integrity of gas and production riser outer sheaths and the gas-venting system •
Topside continuous temperature and pressure monitoring •
Monitoring of produced sand and bore- fuid pressure, temperature and fow rates •
Pressure sheath coupon sampling and analyses •
Monitoring of the turret position and motion and waves oedigital.com June 2015 | OE 41
August.indd 12 7/16/14 2:16 PM 038_OE0615_EPIC1_Jeannie.indd 41 6/1/15 11:20 AM