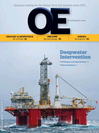
Page 17: of Offshore Engineer Magazine (Aug/Sep 2015)
Read this page in Pdf, Flash or Html5 edition of Aug/Sep 2015 Offshore Engineer Magazine
Field of View 25868-MS, presented at this year’s OTC is often referred to as Anadarko’s largest in Houston. Additionally, other consider- spar built to date by the contractors that ations included the need to avoid landing worked on the development. It is obvious the umbilicals and steel catenary risers this massive project would need assis- (SCRs) in less desirable areas with slopes, tance from the world’s largest support indicating less stable surfaces. vessels.
Ultimately, Anadarko went with a In 2011, Technip was chosen to provide truss spar given its previous experience engineering, construction, and transpor- with the technology on its Boomvang, tation of the Lucius spar hull. A second
Nansen, Gunnison, and Constitution contract followed in 2012, for the devel- developments. opment of the Lucius ? eld. The scope “A truss spar was chosen because it of work included the installation of one could utilize three groups of mooring ? exible ? owline, multiple ? exible gas lift lines, while four group of moorings lines jumpers; main gas lift and in? eld umbili- associated with a semisubmersible would cals; subsea distribution units; electrical,
A view of the 605ft-long, 23,000-ton have been dif? cult to implement given ? ber optic and hydraulic ? ying leads. cylindrical hull of the Lucius spar before it the geotechnical challenges identi? ed on It also called for the design and fabrica- was upended in the Gulf of Mexico in 2013. the site,” Lamey et al. wrote. The moor- tion of the ? exible ? owline end termina-
Photo from Anadarko Petroleum.
ing system consists of nine legs, grouped tion, fabrication and installation of rigid 3x3. The chain mooring lines are secured jumpers, burial of ? owlines, ? ooding and compressor modules, production system, a sacri? cial ? owline isolation valve. A to the seabed with suction piles. hydro-testing of the ? owline system. and fuel gas system were fabricated at clamp-type ? owline connector is used on
Technip’s deepwater pipelay vessel Deep
Additionally, the truss spar for this wet Dolphin Services in Houma, Louisiana. the tree and for all ? owline jumpers.
Blue was used for installation work at the tree-only development was selected to Lamey et al. said the spar hull is
Next up: Heidelberg ? eld alongside sister vessel, Deep Energy.
mitigate site terrain challenges, simplify designed to support the four initial riser design and minimize both cost and Hereema Marine Contractor’s then- Lucius risers and the two initial Hadrian In late June, Anadarko’s Heidelberg truss schedule risk. The Lucius ? eld, along with newbuild Aegir’s ? rst job was to install South risers. Lucius uses four umbilical spar set sail from Ingleside, Texas, to its
ExxonMobil’s Hadrian South – 8mi from risers and ? owlines at the Lucius ? eld, slots while Hadrian uses one. The risers, future home at Green Canyon block 859
Lucius – tie back to the new spar facility. while the deepwater construction vessel Lamey and his co-authors said, have an in the US Gulf of Mexico, some 390mi off
The Lucius project was brought online (DCV) Balder handled the hull and moor- 8.625in outer diameter with 9300psi (g) the Texas coast.
Heidelberg’s topsides, like Lucius, were only three years after it was sanctioned ing commissioning. HMC’s semisubmers- design pressure. Each riser pair has a constructed at the Kiewit yard in Ingleside. and ? ve years after its discovery. ible crane vessel Thalif, capable of lifting control, chemical umbilical and one gas
The pair’s hulls were constructed by
The 110ft-diameter spar was designed 14,200-tonne (15,600-ton), was tasked lift umbilical, the latter will be used for
Technip in Pori, Finland. To reach Texas, for 80,000 bo/d and 450 MMcf/d of natu- with Lucius’ topsides installation. The enhanced recovery and ? ow assurance. the Heidelberg spar sailed 7300nm over 27 ral gas. Reserves will be produced through facility weighed an initial 15,000-ton, The pipeline end manifolds on Lucius days from September to October 2014 on six initial wet tree wells. Lamey et al. said however, the job was broken into nine come with spare connections for future
Dockwise’s Mighty Servant I.
that the hull team and the subsea engineer lifts, the heaviest of which was 10,250- wells, and come with a removable pigging team worked together to develop concepts ton (OE: October 2013). loop to allow for the tieback of additional The 80,000 bo/d, 80 MMcf/d-capacity for pull tubes to support six future risers Allseas’ massive pipelayer Solitare was structures or ? elds. Heidelberg spar is able to operate in water that could accommodate up to 15,000psi used to install an 18in oil export pipe- As part of a contract awarded in 2012, 5300ft deep. It has a maximum topsides riser design for future tiebacks. line, while Saipem’s Casterone handled FMC Technologies supplied six enhanced operating weight of 16,000-ton, and a hull the installation of a 20in gas export line. horizontal subsea trees rated for 10,000ft weight of 23,000-ton. The spar is 605ft
Big support
Allseas’ Audacia installed an oil export water depth and pressures of 10,000psi long with a 110ft diameter.
The Heidelberg development consists of
The Lucius spar has bragging rights. It pipeline end termination in Keathley as well as two production manifolds, and six production wells, the standalone spar,
Canyon 831. associated tie-in equipment.
two drill centers, dual looped 8in ? owlines,
Timothy Dean of Anadarko, Paul
Engineering and subsea development and 16in oil and gas export lines.
Haines of Wood Group Kenny, and
Wood Group Mustang provided front-end
Marsha Calstrom of EXP Engineering Anadarko operates Heidelberg engineering design, detailed design, pro-
International discuss Lucius’ subsea sys- with 31.5% interest. Its partners curement support, and engineering sup- tem in OTC paper 26016-MS, saying the include Cobalt (9.375%), Eni (12.5%), port for the fabrication and offshore con- ? eld was developed with six initial wells ExxonMobil (9.375%), Freeport struction efforts of Lucius’ topsides. Wood split between two 8in nominal produc- McMoRan (12.5%), Marubeni (12.75%),
Group Kenny provided detail design, tion loops, each with a six-well manifold. and Statoil (12%). procurement support, and engineering
An early discovery well is away from support for fabrication and offshore con- the well clusters and Dean et al. said it
FURTHER READING struction concerning the subsea facilities. is daisy-chained into the west manifold
The main model deck structure for ? owline loop. Two other delineation
Watch this video of Lucius’ the topsides was built at Kiewit Offshore wells are produced back to the east mani- topside installation provided
Services’ yard in Ingleside, Texas, along fold with short step out ? owlines, which by Anadarko. http://www.
with the temporary work deck, sub cellar add some ? ow assurance complexity.
oedigital.com/oe-media/ module, and stair tower. The topsides’ The authors say at the core of the sys- oe-videos/item/6204- living quarters were fabricated at Beacon tem are 5x2 10,000psi horizontal subsea anadarko-lucius-topsides-installation
Maritime in Orange, Texas, while the trees equipped with a subsea choke and oedigital.com August 2015 | OE 19 018_OE0815_Field of View.indd 19 7/21/15 2:36 PM