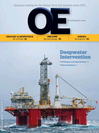
Page 44: of Offshore Engineer Magazine (Aug/Sep 2015)
Read this page in Pdf, Flash or Html5 edition of Aug/Sep 2015 Offshore Engineer Magazine
Pipelines
Corrosion fatigue behavior of high-strength steel wire n the oil and gas industry, ? exible making it cost less. It also has the advan-
Applying materials and pipework has been used for over 30 tage of reduced installation times and corrosion science to the
I years to transport oil-based products being better at adapting to change in ? eld study of corrosion fatigue in from the seabed to ? oating production, layout. storage and of? oading vessels. Flexible pipes are commonly used high-strength steel wire aids
Their ? exibility means that this type in dynamic and static risers, static ? ow ? exible riser performance of pipework can withstand a greater lines, jumpers and expansion joints. understanding. Intertek’s Peter wave loading and that it requires shorter Although suitable for all markets, their
Barnes explains. lengths than rigid-bodied alternatives, versatility and ability to adapt to the changing demands of the offshore oil and gas industry makes them ideally suited to deepwater, ultra-deepwater and the increasingly challenging environments of new ? eld developments.
The structure of an unbonded ? ex- ible pipe, consists of a carcass, an inner liner, pressure armor, tensile armor and an outer sheath. The carcass prevents the inner liner from collapsing while per- forming under high external pressures in deep oceans. It also provides protection against maintenance operations, such as the pigging tools that are used to inspect the pipeline. The pressure and tensile armor layers are both made from carbon steel wire with either a ? at or interlock- ing pro? le.
The region between the inner liner and the outer sheath is termed the annular space. The environment within the annular space can determine the life of a ? exible riser as it can contain corrosive gases, condensed water and seawater.
There are acknowledged to be two main modes of failure of the steel wire. The ? rst is damage to the outer sheath, due to the aging of the thermoplastic sheath or damage during installation, caused either by foreign objects rubbing against it or becoming embedded in the pipe sheath.
This leads to ingress of seawater into the annular space, enabling the corro- sion fatigue process to begin. The second mode of failure occurs when permeation of corrosive gases and condensed water through the inner polymer sheath leads to a corrosive environment within the annular space.
Example of a
Both corrosive environments, com- riser performing bined with the wave loading from the on a platform.
Photo from Intertek. sea, lead to corrosion fatigue failure of
August 2015 | OE oedigital.com 46 046_OE0815_Pipelines1_Intertek.indd 46 7/21/15 9:49 PM