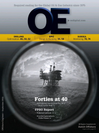
Page 49: of Offshore Engineer Magazine (Sep/Oct 2015)
Read this page in Pdf, Flash or Html5 edition of Sep/Oct 2015 Offshore Engineer Magazine
Visit our stand 4E218 at
SPE
Offshore Europe
Sept 8 -11, 2015
Aberdeen, UK
Leading in development and manufacturing of oil mist separators for combustion engines and turbines.
Emission reduction & increased effciency by the use of highly effcient oil mist separators at crankcase and lube oil tank ventilation.
Walk to work on the West Franklin well head platform. mud. The mud contains particles that plug any micro fractures as soon as it reaches them, strengthening the formation. The most common particles are made from graphite and calcium carbonate.
The important part is the work done to determine the size of particles necessary for each reservoir according to the differ- ent pore pressures, fracture gradients and which zones will be exposed during drilling. Total has a geo-mechanics team tasked with this job. Brian says they have become good at predicting the reservoir characteristics. By interpreting logging data from existing wells and then providing the data required to design the mud needed, which is then procured from Halliburton
Baroid. Total has been using Halliburton Baroid’s Steelseal drilling, because you still need a mud and Baracarb, made from graphite and calcium carbonate, weight heavy enough to balance the respectively.
The world´s only higher pressure formation still exposed The particles range from 5 microns, looking like powder, above,” Brian says. While in theory, to 1500 microns – currently the largest used by Total – which oil mist separator with reservoir zones should deplete at the looks like coarse salt granules. Reaching this size has only
GL type approval same rate, they don’t, creating complex been achieved by the ? rm using the mud over the years and systems that have to be navigated. “You increasing its understanding of what it can do. But it’s not as www.ut99.ch have to ? nd a balance to stop any ? uids simple as using mud with one particle size in it – as fractures coming in, but not so that it is so over- will not form uniformly – a particle size distribution has to
Benefts of UT99 oil mist separators balanced above the pore pressure or be calculated so that the different sized fractures that develop •
Emission reduction, even to obtain EPA Tier 4 fnal fracture gradient that you can fracture can be plugged. In addition, using managed pressure drill- the formation, induce losses or become ing allows the ? rm to more closely navigate the bottom hole •
Reliable increase of effciency at gas / dual-fuel engines differentially stuck.” pressure. •
No deposits on turbocharger
The alternative is to isolate the depleted While using designer mud enables Total to drill through these •
No leakage of oil and oil mist zones, with liners, and carry on drill- sections, because it means there are speci? cally sized particles ing with a different mud weight, but in the mud, it cannot just be recycled after the drilled cuttings •
Long-lasting operational reliability because of the number liners required for are removed. The mud has to be constantly treated before being the multiple zones drilled through, you recirculated back into the well in order to maintain the proper
Key features of UT99 oil mist separators would run out of hole sizes to continue, and designed particle size distribution.
The latest well drilled using designer mud was West Franklin