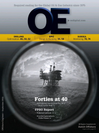
Page 53: of Offshore Engineer Magazine (Sep/Oct 2015)
Read this page in Pdf, Flash or Html5 edition of Sep/Oct 2015 Offshore Engineer Magazine
rigged up the cement head. They pumped Steve Rosenberg is which required 326 bbl. The rupture disc
Drilling a 2 1/8in liner-setting ball downhole the global drilling was blown at 1030 psi, and the top dart to the mechanical ball seat, but several reliability manager latched into the top plug at 351 bbl. The attempts to pressure up and set the for Weatherford’s plug was bumped with 1300 psi of pres- sure, held for 3 minutes, and then bled off hanger were unsuccessful. The hanger Well Engineering and to check that the foats were holding.
was sliding downhole as the slips were Project Management trying to bite into the casing wall, prob- Next, the team performed a liner-top Team with over 30 ably because of the large amount of LCM cement job by bullheading 50 bbl of years’ experience in in the system. The team slacked off and spacer, 75 bbl of 13.7ppg cement, and a the oil and gas industry. He has previ- set the liner on bottom at 13,256ft. further 20 bbl of spacer. They displaced ously worked with Diamond Offshore
The team picked up the string to neu- with 359 bbl OBM at a maximum pres- and Conoco. He holds BS degrees in tral weight, freely rotated at 8000-10,000 sure of 710 psi. Total mud losses during petroleum engineering from Mississippi ft/lb of torque, and released from the both cement jobs was 1139 bbl. State University and biology from St. hanger with 585,000-lb pick-up weight. Finally, the team applied 130,000lb Lawrence University.
They pressured the string to shear the of set-down weight to set the liner top ball seat at 3684 psi and then circulated packer and successfully tested the liner- Ming Zo Tan is the 3 bbl of mud at 225 psi to ensure that the top packer to 1135 psi for 5min. global product string was not plugged. champion for
Conclusion
They performed the liner cement job Weatherford Drilling by pumping 100 bbl of 12.5ppg spacer Weatherford DwL technology isolated the with Casing Product and 3 bbl of 13.7ppg cement along with depleted-sand formation and avoided Line. He joined the bottom dart. Then they pumped potential contingency liners, sticking, Weatherford 12 years another 54 bbl of cement along with the and other delays that would have ago as a DwC top dart and 20 bbl of spacer. This was occurred if conventional drilling means Product Line Manager and held the displaced with 11.6ppg oil-base mud had been deployed. The operation position of Global Application (OBM) until the bottom dart latched into mitigated the expected catastrophic fuid Engineering Manager prior to current the bottom plug, which required 295 bbl. losses and enabled the client to meet its position. Prior to Weatherford, Tan held
The team then launched the bottom plug well construction objectives. The DwL various positions within Halliburton. He with 1150 psi of pressure and continued operation, was completed in 21 hours holds a BS degree in petroleum
ABBTC_ADL2HP_SE_UPGRMARINE_OE 08.07.15 14:37 Seite 1 pumping until it landed on the foat collar, and ahead of schedule. engineering.
Turbocharging upgrades.
The smart move to higher application efficiency.
An ABB turbocharging upgrade utilizes the latest technology to enhance your invest- ment and your engine’s performance. Upgrading your turbocharger will increase your application’s efficiency, thereby saving fuel consumption significantly and increasing your productivity through an increase in your application’s speed margin. What’s more, thus an upgrade increases your engine’s operational life, the time between overhauls, reducing maintenance costs. Make the smart move to an upgrade.
www.abb.com/turbocharging oedigital.com September 2015 | OE 55 052_OE0915_D&C3_Weatherford.indd 55 8/20/15 10:51 AM