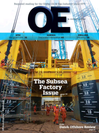
Page 19: of Offshore Engineer Magazine (Aug/Sep 2016)
Read this page in Pdf, Flash or Html5 edition of Aug/Sep 2016 Offshore Engineer Magazine
ABB’s subsea power distribution station, an artist’s impression. Images from ABB. containers to be used on the sea? oor. or more boosting stations, depending on power requirement,
While the project it was meant for was put on hold in 2014, Chene says. “The ? nal arrangement will be a tradeoff between
GE Oil & Gas went through completion of the system, which size of modules, connectors, cable size and size of the units,” successfully completed a 4000-hour testing regime late last he says. year. This resulted in it being “the world’s ? rst system test The aim now is to build on this technology to develop a far incorporating a subsea switchgear and subsea drives.” more compact system, looking at the different materials that
Gilles Chene, senior sales manager, GE Power Conversion, have become available since the project started in 2007, as outlined the project at the Underwater Technology Conference well as progress in power electronics, but also because this in Bergen in June. “For us, the project started in 2007. From system was designed for use with a large compression project. 2009, testing started, followed by integration and, in 2011, “For us now it is about industrialization, not changing the submerged installation at Nyhamna pit [at Shell’s plant],” he technology,” says Kristin Elgsaas, senior product manager, GE said. Testing has been running from 2012 to late last year, he Oil & Gas. “Changing the con? guration so it is easier to as- said, amounting to some 4000 hours, including a 72-hour full semble and reduce risk.” load test.
On show
The system incorporated a 20MVA transformer, switch gear unit, with 35kV circuit breakers and control systems, variable ABB also has a full system ready – in model form for show speed drive (VSD), a 12.5MW, vertically installed compressor at least. The ? rm is working on a US$100 million JIP with and 500kW pump, and other auxiliary systems. The full load Statoil, signed in 2013, to qualify a system able to trans- test ran with 10,100 rpm motor speed. fer 100MW over up to 300km in up to 3000m water depth. “The objective was to ensure a high speed drive could be Chevron and Total are also partners.
created subsea,” Chene says. “It exceeded expectations. The ABB will have a scaled 3D model of the system it is working whole uninterruptable power system (UPS) proved reliable towards quali? cation on at its stand during ONS in Stavanger through the full campaign.” this month [August].
An “ultimate test” saw the system’s fans switched off to test Bugge says that the JIP is going well. ABB is putting its com- performance and this worked, Chene says. While the system ponents in pressure balanced oil-? lled containers, so that they was designed to operate without fans, using natural air circu- can withstand the pressures at 3000m water depth without lation, it was seen that use of fans could prolong operational large, thick containers and make use of cooling mechanisms life. using the oil. “Reliability is key,” he says. These components
A concern around subsea power supply from encased units need to live and operate reliably at 3000m water depth for has been the potentially limited information available as years.
all elements are out of reach, Chene says. To mitigate this, a Currently, the large power and automation ? rm is work- condition monitoring system was put on all units to provide ing on qualifying components, including the power cells, measurements and run different data. which will form part of the variable speed drives. ABB will
As quali? ed, the system could provide power to a hub, then start building the ? rst prototypes this year. Full system from which power could be distributed up to 20km out to 10 testing, covering 3000-hour testing, is due in 2018. Market oedigital.com August 2016 | OE 21 020_OE0816_Feat1_SubseaPower.indd 21 7/23/16 10:37 PM