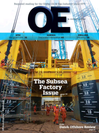
Page 29: of Offshore Engineer Magazine (Aug/Sep 2016)
Read this page in Pdf, Flash or Html5 edition of Aug/Sep 2016 Offshore Engineer Magazine
of the UK’s Technology Leadership Board’s small pools team, then ? ow assurance issues would need to be addressed in case during the NRSI event. “In 1978, Thistle was storing oil in the emulsions form. steel legs of a jacket, with export of crude over a SAL (single Others issues raised include how to handle produced gas and anchor loading assembly), because there was no infrastructure water. Water could be handled, potentially, through treatment in place at the time. The Brent pipeline was still being built. and re-injection, but gas separation and handling remains a
Other examples in the 1970s include Kittiwake. It was the ? rst primary technology challenge, according to a post-event report. asset that had subsea storage over the platform base.” Depending on the ? uids, it could also be that the tank would
There was also Harding in the mid-1990s; Siri, in the Danish have to be heated to prevent wax or slurry formation. sector, in the late 1990s, and most recently, Premier Oil’s One potential solution was to have tank farms. David
Solan. “That is excluding gravity-based structures and big Sinclair, engineering manager, Bibby Offshore, suggests, for concrete structures, or spars,” he says. small pools, having several small tanks, which would be easier
The two main drivers for use of subsea oil storage have to fabricate and install and then recover for of? oading or reuse. “With quicker decline rates on small pools, they could also be been remoteness and a lack of oil export solutions, Whitehead designed to be recoverable for reuse elsewhere,” Sinclair says, says. But, other reasons could include ? eld size, and ? uid and using construction support vessels instead of heavy lift vessels. ? eld complexity – Harding produced a fairly heavy oil and
It would also mean local fabrication could be easier, with fewer it wasn’t possible to just put it in a common network, he says issues relating to concerns around internal integrity, he says. – as well as the succession plan for when existing infrastruc-
This could also mean decommissioning would be easier than it ture becomes too costly to operate. has been for some of the large existing storage tanks.
Most recently, Premier Oil used a steel subsea oil stor- age tank on its not normally manned Solan facility, west
A new business model?
of Shetland, as a way of compensating for the lack of infra- structure in the area. The Solan subsea tank is a beast, using Such a concept could offer the potential 10,000-tone of steel, and measuring 25m-tall, 45m-wide, and for a new business model. Part of the 45m-long, with a capacity of about 300,000 bbl. The tank problem around small pools is that they features a honeycomb of small chambers, containing anodes, are small and fairly widely distributed, so to ensure integrity as waves pass over and to prevent corro- that not one operator has “enough skin in sion on the steel, the event heard. Biocides and biopenetrants the game” said Gordon Drummond, NSRI will also be used to prevent corrosive bacteria and marine manager.
Gordon life from forming. The tank is offset from the steel jacket-sup- Designing one and building many
Drummond ported platform and connected by ? owlines. Premier’s initial would enable standardization and simpli- plans estimated that tanker of? oading will occur every 7-10 ? cation, he suggests. Having a subsea tank as a business akin days, taking 24-36 hours each time. to shipping containers may also address unprocessed ? uids, moving the problem from subsea to onshore where it can be
Scaledown cheaper and easier, albeit it is accepted this would lose the
However, something the size of the Solan tank, which was bene? ts of processing closer to the reservoir and would mean fabricated in Dubai, would not be needed or economical for transporting at least some product with little or no value. a “small pool.” More
Membrane crucially, most subsea tanks, to date, have Norway’s Kongsberg been for use with has been design- processed ? uids. ing a solution – the
Storing unprocessed Kongsberg ? exible ? uids offers signi? cant storage unit. It would challenges. store part-processed
Considerations for oil within a ? exible subsea oil storage membrane, inside a designs for small ? elds protective structure, include ? uid co- providing a double mingling, differential barrier with integral pressure in the tank, leakage control and gas dispersal on ? elds monitoring, says with gas content, slugs Astrid Kristoffersen, dispersal, low en- vice president subsea ergy ? elds and dealing products.
with corrosive ? uids, The ? exible mem-
SeaCaptaur’s monocolumn unit. Image from SeaCaptaur.
Whitehead says. brane helps overcome
Steve Howell, technical director at Aberdeen-based en- differential pressure concerns and also prevents emulsion gineering simulation ? rm Abercus, suggested the storage layers from forming, he says. process could be used to settle out multiphase ? uids – as a The ? exible bag would be made from a coated fabric mem- crude separator. But, he says, some processing would likely brane with a hatch at the top with an inlet and outlet. The bag, still be needed and if water ballasting is used to even out the containing up to 150,000 bbl in a reference case, is attached differential pressure during ? lling and periodic of? oading, to the top and bottom of a center pipe, and both are inside a oedigital.com August 2016 | OE 31 030_OE0816_Feat16_subsea storage.indd 31 7/23/16 11:33 PM