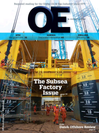
Page 32: of Offshore Engineer Magazine (Aug/Sep 2016)
Read this page in Pdf, Flash or Html5 edition of Aug/Sep 2016 Offshore Engineer Magazine
SUBSEA FACTORYSUBSEA FACTORY
A joint industry project to reduce the time and effort spent on documentation around subsea projects has given the industry food for thought. Elaine Maslin reports.
Paper
Photo from iStock.
shreddingshredding ubsea documentation has really hit a nerve,” companies to comply with the RP or leave, says Roald Sirevaag, “ says Bjørn Søgård, segment director, subsea and project manager for subsea standardization, boosting and com-
S ? oating production, oil and gas, business devel- pression, at UTC Bergen. “It is a sign of what we are achieving,” opment, DNV GL.
Søgård says. “And, it is getting more attention than we had at
Work by DNV GL under a joint industry project (JIP) looking the start. This industry had become expensive and inef? cient. into the documentation shared during subsea project engi-
You have lots of documents shared between vendors and buyers neering revealed some staggering numbers.
and quite a few are ‘for information’ and quite a few for review.
Between 2012 and 2015, subsea documentation increased
The buyer sends back the review documents and the vendor by a factor of four, according to one contractor. Previously, a updates them accordingly. But the trend had become that contractor in a typical subsea project would delivery around documents for information only were also being red-lined and 10,000 documents, with each one averaging three revisions, required updating by the supplier. This was adding complexity.” resulting in up to 30,000 transactions between two actors.
Everything is done for the best intention but, what was happen-
Today, projects can deliver 40,000 documents, with three ing, he says, was that although the market was growing, costs revisions resulting in 120,000 transactions. Handling time has were also growing 15% year on year. In a growth period this also doubled per revision. creates more talent mobility in the market and as staff turnover
The result is cash, in staff and time. The JIP addressed the increases, reducing the number of staff with knowledge of proj- issue by looking at what documents were necessary and what ects, which continues the cycle. added cost without adding value. The idea, which resulted in
Another factor driving cost in this area has been operators a recommended practice (RP), is to de? ne what needs to be adding their own requirements on top of the routines vendors shared, and what doesn’t, and where some documents can be were already working to, including welding procedures, forging standardized. systems, etc. In the maritime industry, this isn’t such an issue as
One JIP participant thinks that by adopting the subsea doc- buyers trust the yards thanks to governance procedures estab- umentation RP, a 42% reduction in engineering hours could lished by the class societies. Maritime suppliers making com- be delivered, by reducing reviews through reuse of docu- ponents know how they need to be made and how quality will ments and having more standardized documents and avoid- be assessed,” Søgård says. “This isn’t the case in the offshore ing unnecessary reviews on non-critical documents. Another industry. We need greater governance and trust.”
The industry is taking the RP on board, however, he says, and member of the JIP thought up to 70% reduction in amount of
DNV GL is also looking to take it over to the UK sector, where it documentation could be delivered.
A draft version of the RP was used on Statoil’s Johan Sverdrup is in discussion with the Ef? ciency Task Force, a group set up to project last year. The Norwegian oil major leaned heavily on drive ef? ciencies like subsea documentation standardization.
August 2016 | OE oedigital.com 34 034_OE0816_Feat7_Documentation.indd 34 7/23/16 9:48 PM