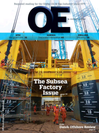
Page 51: of Offshore Engineer Magazine (Aug/Sep 2016)
Read this page in Pdf, Flash or Html5 edition of Aug/Sep 2016 Offshore Engineer Magazine
Subsea 7’s ? owline solutions (from left: moment capacity and residual out- require corrosive resistant alloy (CRA) upheaval or lateral buckling and walking-
SUBSEA bundle, direct electrical heating pipe, wet of-straightness (OOS) of the pipe will lined pipe for the inner pipe. Under gradual axial displacement of the whole insulated pipe, electrically heat traced change depending on the load transfer these conditions, however, the PIP pipeline towards one end or buckle sites ? owline, pipe-in-pipe, lined pipe and between the inner and outer pipe as- system can be installed using reel-lay creeping from their originally formed single pipe). Image from Subsea 7.
sociated with each method. Post-lay, with fresh water in the pipe, so that the positions, the paper says, resulting from the carrier pipe is fully straightened. internal pressure will prevent wrinkles pipe-soil interaction, seabed slope, axial
However, the ? owline is more sinusoi- in the CRA pipe from forming, despite ratcheting, and residual bottom tension. dal when using reel-lay, rather than the compressive forces induced dur- To mitigate buckling, the pipeline
S- or J-Lay methods. Also, during ing installation. The solution has been can be “snake laid” to form control sites installation, with the vessel’s tension- successfully applied during the installa- for buckling, laid over sleepers, spot ers carrying the carrier pipe load and tion of single lined pipe for the Guara- rock dumped, or buoyancy units can be the vessel’s equipment carrying the Lula project, and according to the OTC strapped to the pipe to supplement the ? owline load, a residual axial compres- paper authors, the same solution can be formation of seabed induced buckling, sive load is induced on the inner pipe adopted for PIP systems with CRA lined say the paper authors. The curved that has been laid on the seabed. When inner pipe. During normal operations, section of the snake lay are triggers this compressive installation stress is the high temperatures can also cause for buckle mitigations, as well as the combined with the hoop stress induced wrinkles, however, the effects of high sleepers and buoyancy units. To prevent by high internal pressures and the temperature are overcome by the high excessive loading on riser connections, operating conditions, a high equiva- pressure, during operation. Though, spools, and jumpers, walking tendencies lent stress close to the pipe’s yield wrinkles can form when the system is can be mitigated by tying the PIP system stress can develop, according to the shut-in and compression is induced due to suction piles or anchoring the system paper. Factor in the differential axial to the pressure dropping quicker than with clump weights and tether clamps.
load and bending moment capacities the temperature. But, if the residual cur- The pipeline bundle system expands of a section – a result of the variations vature of the pipe has a nominal strain the limits of HPHT ? owline design, the in yield strength and wall thickness of 0.4% or less, the issue can be avoided; high axial compressive forces generated due to manufacturing process – and a otherwise, a minimum internal pressure by the high termperature are balanced localized axial deformation, wrinkling of 7-10 bar may be necessary to mitigate by tension in the sleeve and outer car- of the inner pipe wall, and eventual wrinkling issues during shutdown, says rier pipe. The balanced forces with failure of the inner pipe can occur, the paper authors. the added weight of the bundle system particularly at weak sections. High temperatures in the system can mitigates the need for global buckling
Installation causes stress on the car- also affect the centralizers and thermal mitigation measures and therefore offers rier pipe, as well. During installation, performance. Exposed to high tempera- a cost ef? cient alternative solution.
tensioners induce tension on the carrier tures, the centralizers can be suscep- HPHT ? elds can be demanding on the pipe, and when the pipe is laid on the tible to thermal creep and progressive equipment used to produce from them. seabed, the tension is gradually relieved deformation. This deformation can then Engineers not only need to be concerned and the carrier pipe goes into compres- lead to the insulation deforming, which with the impact of ? uid properties on sion. At the same time, hoop compression would affect its performance. host facilities, but also the properties
How PIP systems are installed also resulting from the hydrostatic pres- of the pipeline used to transport them, needs consideration. Generally, a PIP sure causes small axial tension, due to and the condition in which the pipe is system can be trenched and buried,
Poisson’s ratio effect that will act together installed. completely rock dumped, or just laid on with the installation induced stresses, * Sriskandarajah, T., Ragupathy, P., the seabed. But, as water depth increases, outlines the Subsea 7 OTC paper.
& Rao, V. (2016, May 2). Design Aspects trenching and burying and rock dumping
Corrosive tendencies of Pipe-in-Pipe Systems for HP-HT become prohibitively expensive. Along
If the ? uids produced from the HPHT Applications. Offshore Technology with how the pipe will be laid, engineers ? eld are corrosive, the PIP system may Conference. doi:10.4043/27046-MS must also mitigate the pipe’s tendency for
Seal your pipes without welding
Use the innovative non-weld Roxtec SPM™ to seal metal pipe penetrations against fire, gas and water.
O Protect life and assets O Save time and money O Speed up installation
Read more on www.roxtec.com oedigital.com August 2016 | OE 53 052_OE0816_Subsea_jl1.indd 53 7/23/16 12:29 AM