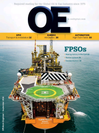
Page 18: of Offshore Engineer Magazine (Sep/Oct 2016)
Read this page in Pdf, Flash or Html5 edition of Sep/Oct 2016 Offshore Engineer Magazine
then successfully on Bravo earlier this year. The 2D sonar im- Able UK, in northeast England, had to upgrade its quayside age was converted to a 3D model, which then allowed Shell to in order to receive the topsides, with some 1200 piles in- model the quantity of sediment. stalled then covered in a concrete pad ready to receive Delta’s
The external sampling tools and the sphere con? rmed some topsides. Able will also lead recycling efforts, hoped to reach 4m deep of sediment. The sediment was made up of 25% sand, 97%, with a level of re-use. Able already has designs on the 25% oil and 50% water. galley and that elements such as valves are likely to be reused,
Now the attic oil is being successfully siphoned out. To make more and more so when this market grows, Hope says.
FIELD OF VIEW sure it is all removed, it is measured using a conductivity tool,
Cleaning up to see when the attic oil stops coming through and it turns to
It’s not just about the platforms. Shell also has some 28 pipelines, the ballast water, as well as a UV light. While the work is being including umbilicals and ? exibles, to done through the platform moon pool, when deal with, measuring from 2.5-36in in the topsides are removed, it could also be diameter, on a case-by-case basis, with done from a support vessel. either removal or ? ushing and burial.
Heavy lifting
And even then, clean-up work will be
One of the next steps will be more vis- needed around the platforms, to clear ible – the Delta topsides removal in 2017. all debris, such as scaffolding, broken
It’s a year late, due to commissioning on off during severe weather. the Pioneering Spirit lifting arms taking
Life goes on “longer than anyone anticipated,” (OE:
Delta will be the ? rst topside to be
April 2016 and August 2016). Shell’s Hope
Going into inner space, removed in the campaign, in 2017, describes the work on each arm as being with the help of NASA. with three more to come, as well similar in complexity to commission-
Photos from Shell.
as completion of the P&A program. ing a small southern North Sea platform,
Lessons learned in this project will and then all 16 arms work together, but be passed on, Manning says. “Some of also act independently. However, the this is about driving greater ef? cien- delay will not impact Shell’s operations, cies in delivery,” he says, “conducting
Manning says. The vessel has already planning and execution and prepara- successfully performed a test lift. And, as tion early. Some of it is about ensuring
OE went to press in late August, the ves- the platform is prepared for end-of-life sel completed the Yme topsides removal activity, that cranes are robust, there’s offshore Norway.
The Delta lift will involve the Pioneering robust power solutions and you’re
Spirit bow slot ballasting into position not reliant on reservoir gas to provide beneath the topside, before using 16, power. Some of it is ensuring there is
Pre-deployment testing. 65m-long, lifting arms to lift the platform the right focus on the platform.” from its base. It’s an ambitious system, but
There’s also scope for new tech- one in which Shell has con? dence, having nology to come in and impact how done its own studies on the design prior to decommissioning is done, not least in signing a contract for the unit in 2013. the P&A space, which is nearly half the
To do the lift, however, reinforce- total cost of decommissioning. “Being ment work had to be carried out on the able to P&A more ef? ciently so you can topsides. Eight cruciform lifting points, abandon a well in one run would be weighing 120-tonnes in total, had to be the dream ticket,” Manning says. “We added to the underside of the platform, are tracking a number of technologies for the mating with the Pioneering in the P&A space with various levels
Spirit’s lifting arms. Structural reinforce- of technology readiness and expecta-
NASA’s survey ment was also added to the lower decks. tions.” The issue here, he says, is ? nd- tool up close.
Three shear restraints, at around ing test wells for these technologies. 12m-diameter and weighing about 36-tonne each, have also Doing it 186km offshore in the rough northern North Sea isn’t been installed in each leg, to hold the platform in place after perhaps ideal. More broadly, doing things quicker and more leg cutting, by Cut UK. They will also accommodate the shear ef? ciently is an all-round goal, he says.
But, it’s not all about decommissioning. In order that ? elds, forces during the lift, Manning says. “They effectively make which currently produce over the Brent facilities, i.e. the the cut legs as strong as they were before the cuts,” Hope says.
Penguins development, which produces through Brent Charlie,
Based on the Delta lift plan, eight lifting points were added,
FLAGS (Far North Liquids and Associated Gas System) pipeline, two more than the six originally thought necessary. The 16 are not left stranded, a bypass route is due to be installed. lifting arms will also be acting in pairs (two for each lifting
The facilities will also require periodic inspection, some- point), Hope says, adding further redundancy. It’s a conserva- thing that could be well-suited to autonomous underwater ro- tive approach for the ? rst lift. “We are actually looking at how botics, which could swim out from onshore, Manning suggests. we can make this less conservative in the future, as there is
It’s a future technology, but one which could have use here. We substantial conservatism in this,” he says. look forward to reporting on it, when the time comes.
Others have also had to invest to make this project happen.
September 2016 | OE oedigital.com 20 017_OE0916_Field of View_jl1.indd 20 8/23/16 6:31 PM