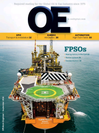
Page 44: of Offshore Engineer Magazine (Sep/Oct 2016)
Read this page in Pdf, Flash or Html5 edition of Sep/Oct 2016 Offshore Engineer Magazine
Point of no return –
SUBSEA injection accuracy
In the subsea environment, accuracy of inhibitor dosage is paramount. The
PULSE LF CIMV increases ? owmeter accuracy and inhibitor dosage. Image from
Schlumberger.
Effects of incorrect chemical dosage
Problematic and costly repercussions can occur should the inhibitor dosage be over or under the optimum applica- tion rate. Reasons for under- or overdos- ing are often tied to chemical injection ? owmeter accuracy, which can be heavily in? uenced by the properties of the injected chemicals. Under injection of treatment chemicals can result in scale or paraf? n buildup in well produc- tion strings or pipelines, lowering the production rate. If the scale or paraf? n exist in the line for an extended time period, the well may have to be shut in to undergo a batch treatment, incurring deferred production and intervention costs. Where corrosion inhibitors are being injected, subsea umbilicals, risers, and ? owline (SURF) facilities can, in severe cases, be take n of? ine until failed components are replaced.
In the case of overdosing, chemi- cal excess costs can be signi? cant and the additional chemical tanks take up valuable deck space on the platform.
For instance, a company could spend more than US$1 million to overinject just one well over the life of the ? eld.
Furthermore, excess levels of LDIs in the export crude may affect its value at
The dawn of ultrasonic ? owmeter technology increases the re? nery. Over the life of a ? eld, ac- curate ? ow measurement and control of chemical dosage accuracy, says Cameron’s David Simpson.
LDI injection could reduce operational or low-dose inhibitor (LDI) injec- ? eld life could become over injected by expenditure by tens of millions. tion on long step-out, deepwater as much as 3-4 million liters of excess
F The challenges of metering LDIs tiebacks or satellite wells, the chemical based on the selection of CIMV subsea chemical injection metering technology. With LDI injection, particulate block- valve (CIMV) is the point of no return. In long step-out deepwater projects age is a recognized cause of CIMV
Pinpoint accuracy of injection is not with complex system architectures, LDI failure; this blockage is partly caused only critical to achieving full inhibition, injection and control can be prob- by the extremely low required injec- it can save operators from pumping large lematic. Subsea distributed chemical tion rates, sometimes less than 0.5 L/h volumes of excess chemical over the life injection is often best suited to address [3.17 gal/d] and the fact that particulate of the ? eld just to protect from chemi- the ? ow assurance challenges of these contamination can be introduced into cal injection ? owmeter inaccuracy. A wells, but requires greater control and the chemicals during transport, storage, typical ? eld in which LDIs were injected accuracy over levels of LDIs being and subsea distribution. These particu- at 2 L/h into 12 wells over a 20-year added, at multiple points, into the ? ow. lates can block moving parts inherent to
September 2016 | OE oedigital.com 46 046_OE0916_Subsea3_CameronSLB.indd 46 8/23/16 4:56 PM