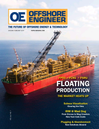
Page 9: of Offshore Engineer Magazine (Jan/Feb 2019)
FPSO/FNLG Outlook and Technologies
Read this page in Pdf, Flash or Html5 edition of Jan/Feb 2019 Offshore Engineer Magazine
LEADING OFF Visualization Technology
Pretty – measurable – pictures which is collected as point cloud data, is then carried out to
On the ? y surveys are being done using photogrammetry. In reconstruct the site or object in a 3D model to mm accuracy.
summer 2018, Comex Innovation completed two North Sea offshore inspection projects using its ORUS3D underwater Automated eventing photogrammetry technology, having previously done projects EIVA has been working on the use of machine learning and in West Africa, Raymond Ruth, U.K. and North Sea Agent computer vision techniques to detect objects such as anodes for Comex Innovation, said. Both operations, in the U.K. and on pipe, pipe damage and marine growth automatically, us-
Danish sectors of the North Sea, called for high accuracy mea- ing a conventional camera, said Matthew Brannan, senior sur- surement, one in support of brown? eld modi? cations. veyor, EIVA. To use machine learning means having to train a
The ORUS3D subsea optical system measures and then system with tens of thousands of images from pipelines. This creates high-resolution 3D models of subsea structures. Each is what EIVA has been doing, and it’s bearing fruit. The com- system comprises an integrated beam of tri-focal sensors, with pany has run trials on existing data sets that were evented the four wide beam LED ? ash units, plus a data acquisition and traditional way, so it was possible to compare the automated processing unit. It uses triangulation of features within the im- results with the manmade eventing. Late 2018, it also started ages captured to localize its relative position and build a 3D live testing during ROV-based operations. The ultimate aim point cloud reconstruction that can be used for measurement, for the technology is for automatic event recognition during so that an inertial navigation system or target placement on the an AUV survey, enabling an AUV to spot something and then object for scaling are not needed when on site. send a message to a surface vessel, Brannan said.
The integrated unit ? ts on to an ROV for free-? ying data EIVA is also taking conventional cameras further, using si- acquisition from more than 40cm away from structures, al- multaneous location and mapping (SLAM) and photogram- though the best distance is between 1-2m from the object. metry to do map areas, while being able to locate the camera’s
This takes no longer than a general video survey, Ruth said. position relative to what it is mapping. Existing SLAM sys-
Initial onboard real-time processing is carried out to assess tems rely on loop closure, and photogrammetry solutions need location and quality, before onsite (on the support vessel) pro- a lot of image overlap and good visibility, and are usually not cessing, to further quality check the data and create an initial real-time, Brannan explained. Some also rely on costly stereo scaled 3D model to cm accuracy. Final processing of the data, cameras, which need calibration and take up space, he said.
Results from an
ORUS3D survey.
INSET Rovco’s live
SubSLAM concept.
Source: Comex Innovation; INSET Source: Rovco
January/February 2019 OFFSHORE ENGINEER 9 1-17 OE 2019.indd 9 1-17 OE 2019.indd 9 1/21/2019 3:58:42 PM1/21/2019 3:58:42 PM