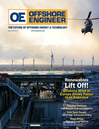
Page 51: of Offshore Engineer Magazine (May/Jun 2019)
Offshore Renewables Review
Read this page in Pdf, Flash or Html5 edition of May/Jun 2019 Offshore Engineer Magazine
THOUGHT LEADERSHIP Class & Regulations “MOST OF TODAY’S
OFFSHORE FACILITIES
ARE MANAGED BY
INDUSTRIAL CONTROL
SYSTEMS DESIGNED WITH
EFFICIENCY IN MIND RATHER
THAN SECURITY.”
MARK TIPPING
OFFSHORE TECHNOLOGY
MANAGER, LLOYD’S REGISTER
Source: Lloyd’s Register of which clearly demonstrated the potential bene? ts. We believe no manning. In conclusion while new technology, such as digi- remote survey can provide immediate operational improve- tal health management and maintenance analytics provide the ments such as optimized scheduling, which helps to foster an key to unlocking these opportunities, it is their linking to the old ef? cient survey process for class and owner alike. technologies which will prove fundamental to success.
TIPPING: In terms of focused R&D, the agenda is to take cost HOVEM: There are a couple of projects for offshore which out of operations without negatively impacting safety. Hence come to mind. WIN WIN is DNV GL´s concept for a new the push is to reduce or eliminate the permanent manning of generation of oil recovery technology. Using a wind turbine to facilities in continuous production operations. This drives to the power water injection systems will reduce costs, increase ? ex- development of systems that have the reliability and resilience ibility and avoid CO2 emissions. The oil and gas industry is for long-term isolated operation, this however is not as simple under signi? cant pressure to reduce both costs and emissions as deploying advanced control systems, it comes down to a ful- from extraction activities. Maximizing oil recovery from new ly integrated design and operations philosophy that to date has and existing ? elds is therefore of paramount importance. Wa- struggled to bridge the capex and opex project phases. ter injection is a frequently used and highly effective means
Not only does equipment need to be selected for long service of improving oil recovery from oil reservoirs. However, con- life with minimum intervention but also how this can be accom- ventional methods entail high power consumption, signi? cant plished in discrete maintenance windows. The best solution is emissions and costly infrastructure.
to eliminate the need for equipment, however where this cannot Secondly, we have developed a new a solution that reduces be done for example elements exposed to the marine environ- the risk of offshore ? oating vessel mooring line failure going un- ment new approaches to how we consider ef? cient design occur; detected by replacing physical sensors with a machine learning for example the hull of a ? oating facility might be considered algorithm that accurately predicts line failure in real time. The for optimization to reduce steel weight – however in operation DNV GL team developed the Smart Mooring solution by train- this may lead to higher stress values, greater criticality around ing a machine learning model to interpret the response of a ves- corrosion and a consequent higher cost of ownership which is sel’s mooring system to a set of environmental conditions and are especially impactful if the intent is to operate with reduced or then able to determine which mooring line has failed.
MAY/JUNE 2019 OFFSHORE ENGINEER 51 50-64 OE MayJune 2019.indd 51 6/10/2019 10:26:19 AM