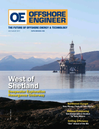
Page 34: of Offshore Engineer Magazine (Jul/Aug 2019)
Subsea Processing
Read this page in Pdf, Flash or Html5 edition of Jul/Aug 2019 Offshore Engineer Magazine
FEATURE Subsea Processing
The subsea compression system in
Egersund,
Norway before sail away to the
Åsgard feld.
Source: Aker Solutions ? ow rates up to 18,000 cubic meters per hour, per compres- the FEED phase and going “full steam ahead”, Nyborg said. sor. The topside electrical variable speed drives and the subsea After delivering Åsgard, Aker Solutions’ lead engineers transformers for both the compressors and the pumps were from the project, together with help from separate alliance provided by ABB. Aker Solutions also delivered the topside agreements with MAN Energy Solutions and ABB, employed power and control module for the Åsgard A ? oating produc- their experience and lessons learned to develop a next gen- tion, storage and of? oading unit (FPSO) to power the com- eration subsea compression system, SCS 2.0, for new ? eld pressors and pumps. developments, including Jansz-Io. The companies managed
To date, the Åsgard subsea compressors have run for more to maintain their core teams and competencies through the than 60,000 hours with close to 100% reliability, and it is es- downturn, already underway when Åsgard went on stream.
timated that the solution will enable more than 300 million According to Nyborg, “The main objective of the SCS 2.0 barrels of oil equivalent to be recovered from the ? eld. program has been to reduce cost, size, weight, complexity, de- livery time and also the need for heavy lift operation, while keeping the core functionality and robustness in design.” He
New fields
Now Aker Solutions and its partners are working to advance said, “The engineering work performed indicated that the SCS 2.0 system is able to realize more than 50% reduction in terms the technology even further as they look to take subsea com- of total size and weight.” pression projects into new waters.
“Take the compressor module for example, utilizing the les-
Located around 200 kilometers off the Australian northwest coast in approximately 1,350 meters water depth, Jansz-Io, part son learned – the module size and weight were reduced from of the Gorgon project – one of the world’s largest natural gas 294 tons to 180 tons. One way this was done was by simpli- developments – will mark the ? rst use of subsea compression fying the module pipe routing and by moving the anti-surge technology outside of Norway. The project, led by operator function out of the compressor module. Compared to Åsgard
Chevron with partners ExxonMobil and Shell, is currently in the number of modules has been reduced from 13 to seven per 34 OFFSHORE ENGINEER OEDIGITAL.COM