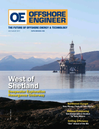
Page 36: of Offshore Engineer Magazine (Jul/Aug 2019)
Subsea Processing
Read this page in Pdf, Flash or Html5 edition of Jul/Aug 2019 Offshore Engineer Magazine
FEATURE Subsea Processing including reduced equipment costs, better delivery time, min- ABB and MAN Energy Systems. We have also been focusing imized heavy lift operations and design robustness to limit on critical sub-suppliers as a continuous process, not just for maintenance operations. speci? c projects,” Nyborg said.
“Åsgard subsea compression was the ? rst subsea compres- In addition to performance gains, another bene? t of subsea sion delivery anywhere. The modularization philosophy for compression at Jansz-Io is improved environmental footprint
Åsgard was to keep all main process equipment individual over the life of the ? eld. Nyborg said, “Getting the compres- retrievable from the station, and the consequence of this was sor closer to the well offers big advantages compared with separate modules for each of the main process units, in addi- alternative solutions (compression platform or onshore com- tion to a spool interface module. This gave us a robust design, pression). Our updated subsea compression system can offer but also substantial weight and size,” he said. increased recovery, less power consumption, offshore logis-
Since Åsgard, the lead engineers have been focusing on tics elimination, no discharge or emissions, with less material implementing the low/no risk opportunities that are spotted used. The weight of the Jansz-Io system will be signi? cantly in the project execution and design, Nyborg said: “For exam- lower per MW compression compared with Åsgard.” ple, the reduction of the process modules from seven to three Nyborg said Aker Solutions has developed a set of perfor- results in a signi? cantly reduced footprint of the compressor mance indicators that will be used to measure the environ- train. Heavy lift operations are minimized by reducing the mental impact of products and system solutions in a project weight of the modules.” or product development. Due to launch this year, the indica- “Delivery time is improved by the fact that we have done tors will be incorporated in the Jansz-Io project to measure this before. It is all about the knowhow and experience of the the ef? ciency of boosting, material consumption and inter- team, as well as the strength of the alliances we have with vention frequency.
Standardized Subsea Processing
When used under the right circumstances, subsea process- and now, after several years, the partners have completed ing technologies have clear and obvious bene? ts as an enabler phase two, resulting in guidelines converted to DNV GL rec- for increased oil recovery and even as a more environmentally ommended practice (RP) and shared with the broader industry friendly alternative to conventional processing equipment. outside of the JIP group for comments ahead of publication in
In many instances, however, operators have found these solu- early autumn 2019.
tions to be too expensive to implement. The number of projects The goal is to make subsea pumping a more competitive with subsea processing that have been sanctioned to date are far option through standardization and alignment of technical fewer than what operators would like, because of the cost level, requirements, de? nitions, work processes and documenta- said Kristin Nergaard Berg, a principal engineer at DNV GL. tion. The RP examines standards, functional requirements
With this in mind, DNV GL, working alongside suppliers and speci? cations; system design; pump modules and pres-
Aker Solutions, Baker Hughes GE, OneSubsea and Technip- sure containing equipment; control system and instrumenta-
FMC and operators Petrobras, Shell, Equinor and Woodside, tion; power systems; materials and welding; and quali? cation kicked off a joint industry project (JIP) in 2015 aiming to use work processes and test requirements. “The key is that we standardization as a means to reduce the lifetime cost of sub- have looked into the whole subsea pumping system, including sea processing equipment for use globally. several disciplines trying to ? nd ways to lower the cost in each
Berg, the JIP project manager, said the partners initially and every discipline,” said DNV GL’s So? a Wilhelmsson.
looked at the “big scope” of subsea processing technologies, What kind of cost and time savings can be achieved? It’s including pumping, compression, seabed separation and injec- still a hard question to answer. “The real bene? ts will ? rst be tion, but decided to focus on pumping because it’s the one tech- seen when the document is taken into use. There’s no bene? ts nology most operators were interested in and it’s by far the most or cost savings in a piece of paper,” Wilhelmsson said. The mature of the group – meaning more experience to draw from. hard numbers will come through implementation and experi-
The JIP’s ? rst phase outlined the plan for standardization, ence after the RP guidelines are put to use.
36 OFFSHORE ENGINEER OEDIGITAL.COM