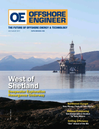
Page 49: of Offshore Engineer Magazine (Jul/Aug 2019)
Subsea Processing
Read this page in Pdf, Flash or Html5 edition of Jul/Aug 2019 Offshore Engineer Magazine
Engineering, Procurement, Installation & Commissioning 3D Printing
Source: Total revealed then shipped to Port Harcourt within 48-hours and be made,” he continues. “Tiny holes can be made to measure then sent offshore. Using a remotely operated underwater pressure at speci? c locations. These holes you cannot ma- vehicle (ROV), the plunger was unbolted and then the tool chine. But you can embed them precisely to allow you to do used to inject methanol, dissolving the hydrates in the pipe monitoring and pressure monitoring of a part. Third, you can and successfully allowing the pressurized plug to be removed do in-situ repairs to parts.” within four hours. Greder says that, for Total, this is something new and valu- “It was 10 days from design to delivery, 50% lighter than able in the ? eld, and it’s happening more. “Several impel- expected, and the cost was reduced by a factor of 10 com- lers have been made and put in re? neries in France,” he says. pared with a conventional subsea operation for this kind of “On the Culzean production facility in the UK North Sea, we problem, that would have cost more than €10 million,” says 3D printed some titanium alloy inducers for installation on
Greder. Akpo production also didn’t have to be halted and the transfer pumps.” The modi? ed impellors helped to counteract gas export line was connected on schedule. cavitation and could be produced quickly, instead of taking 24 “Using additive printing means it’s topologically optimized. weeks, using traditional methods.
You can have shapes close to what nature can offer us, like “This will grow,” concludes Greder. “AM will certainly a bee nest,” Greder says. By using this approach more, lead disrupt the oil and gas supply chain. More work needs to be times, nonproductive time and production short-falls can done on quality of the material; you’re creating a part at the be reduced. “In future, I can imagine a printer in Aberdeen, same time as creating the shape. Before, you were working
Stavanger, Bergen, where you can send a ? le and they print a on material that was created then the shape was certi? ed. So tool you need and send it offshore. If you can do it on demand, there’s work to be done around certi? cation of material and you can also save storage cost. repeatability. There’s also intellectual property, if you want a “Another advantage is that compact sophisticated parts with copy of a part. For the time being, we have started using it on more functions, lighter weight and easier to instrument, can non-critical parts. But it will come.”
JULY/aUGUST 2019 OFFSHORE ENGINEER 49