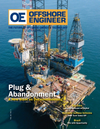
Page 41: of Offshore Engineer Magazine (Sep/Oct 2019)
Big Data and Digitalization
Read this page in Pdf, Flash or Html5 edition of Sep/Oct 2019 Offshore Engineer Magazine
Quick clay liqui? es when agitated
Source: Encompass ICOE
Sticking with cement Testing, testing, testing
Some companies are looking to stick with cement, but to A challenge for new design well barrier materials is the cri- improve it. Well-Set, based in Norway, is looking at magneto teria they must meet. Cement has been used for decades and rheological cement. This involves using traditional cement but is the default, even if it’s not perfect, as some assert. If other controlling how it is set – its rheology – more accurately by im- materials are to be used, they need to be proven. One chal- pregnating the cement with magnetic particles then using a mag- lenge is exactly what they need to be proven to do. netic ? eld to place it, says Banks. It’s similar to a process used Another challenge is that current criteria for well barrier in car suspension where a magnetic ? eld hardens the suspension materials are based on cement. “If we were to apply the same hydraulics for “sport mode”. The OGTC has supported a desktop scrutiny to cement that applies to new materials, cement plugs study with Well-Set and is now moving to a Phase 2 project, sup- would struggle.” says Brian Willis, research and development ported by ConocoPhillips, involving full scale and bench testing. engineer at Astrimar. “The requirements are still very much
Meanwhile, at the University of Strathclyde, Glasgow, written with a cement mindset. Quali? cation is done against nanoparticulate silicate and biogrout technologies are being the values and strength of cement as opposed to how a plug looked at. “Cement, over time, will shrink, crack and de- functions as a barrier. Not enough is being done to understand grade,” says Banks. “The ability in the annulus to retain the how new plugs might fail and how that may affect performance barrier long term is something that’s a concern to industry.” in sealing a well and remaining in place. That means there are
Especially as there’s no way to go back in and repair it. So, materials that have gone through recommended quali? cation ideas from civil engineering are being looked at, including and ? eld trials and which are now experiencing issues and it’s biogrout, which uses enzymes that deposit calcium carbonate hard to ascertain what’s going wrong because early quali? ca- in the downhole environment. “The nanoparticular silicate, tion testing was not as extensive as may actually be required.” meanwhile, would get into the cement or cracks where it gels Astrimar has developed a STEM-? ow predictive analysis and, while hasn’t got compressive strength,” says Banks, “it tool to help assess the predicted life of barrier materials and has pressure retaining capacity so it helps to seal areas in a P&A designs. It’s been created based on a database of materi- well bore that might otherwise ? ow.” als, including cement, built by Astrimar following extensive
Another cement adaptive technology is being developed by data gathering. It was used as part of Rawwater’s product de-
UK-based Resolute Energy Solutions, who are testing using velopment. “With the addition of extensive TRL4 testing, the additives in cement that expand downhole to eliminate shrink- predicted life of the bismuth alloy compared with cap rock was age. They’re on the OGTC’s TechX program, to help acceler- improved greatly,” says Willis. But, he stresses, it’s not just ate their work. about the material that’s deployed, it’s also about the interfaces
SEPTEMBER/OCTOBER 2019 OFFSHORE ENGINEER 41