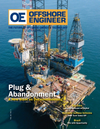
Page 44: of Offshore Engineer Magazine (Sep/Oct 2019)
Big Data and Digitalization
Read this page in Pdf, Flash or Html5 edition of Sep/Oct 2019 Offshore Engineer Magazine
FEATURE Dr illing
The
Drilling
Source: © Mohammad Fahmi Abu Bakar/Shutterstock
Evolution
By Jennifer Pallanich ollowing a few years of low oil prices and a drop in rig have a better idea of the health of that asset,” Rousseau says.
utilization rates, drillers remain focused on ways to im- Knowing the health of an asset is vital for condition-based
F prove operational ef? ciency and safety. monitoring and makes it possible to move away from the calen-
Many of the improvements to rigs are evolutionary, such as dar-based monitoring that may require looking at every piece of automation, remote control and sensing, and how rigs make machinery once a year and tearing it apart at certain intervals.
sense of the vast volumes of data generated by sensors. The “The drilling rig is there to drill,” he says. “You want to interconnectedness of all those sensors raises cybersecurity minimize that nonproductive time, the time you’re not spend- concerns, while environmental concerns have led some drill- ing drilling that hole or moving onto the next one.” ers to investigate energy-ef? cient methods to power their op- Sensors can monitor temperature, pressure and vibration erations. Newer technology like managed pressure drilling among other things. There’s a continuum of digital sophisti- (MPD) is making its mark on rigs, and a 20K drillship brings cation, he says, which moves from piecemeal monitoring to a step change to the industry. real-time monitoring.
“There’s a lot of focus on operational ef? ciency,” says Jo- “You can get ? ooded with data and not know what to do seph Rousseau, ABS director for offshore exploration. with it, or have no data at all. Neither is a particularly good
One way to vastly improve operational ef? ciency and safe- place,” he says. ty levels is through automation such as iron roughnecks and Big data, analytics and computer modeling can parse in- pipe handling. coming data in real time to generate alarms if a machine is out “If you can remove humans from a dangerous spot like the of tolerance. drill ? oor and do that with a robotic controlled machine, you Smart technologies will go beyond collecting the informa- don’t have humans in pinch points,” Rousseau says. tion in real time so it’s possible to act on. Eventually, he says,
Remote control also makes operations safer. the industry will be able to predict problems a month or two “The drill ? oor equipment used to involve a lot of people ahead of time so the asset manager can plan maintenance be- working in that industrial area. Now it’s driven from the drill- fore the equipment fails.
er console,” he says. The upshot, Rousseau says, is that information from sensors
More and more sensors are being built into drilling rigs and enables decision making “based on data instead of looking at the equipment that goes on them. a calendar and saying, ‘I guess it’s time.’ The rig spends more “If you put in the right sensors and measurement systems, you time working and less time doing ancillary tasks of inspecting 44 OFFSHORE ENGINEER OEDIGITAL.COM