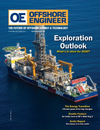
Page 51: of Offshore Engineer Magazine (Nov/Dec 2019)
Exploration Outlook
Read this page in Pdf, Flash or Html5 edition of Nov/Dec 2019 Offshore Engineer Magazine
CASE STUDY CannSeal
CannSeal Unlocks Development of an
Additional Reservoir by Restoring Integrity to an Unconventional Cement Packer Design
Source all images: CannSeal
Annular isolation technology specialist CannSeal aided penetration with max reach topside to occur, while not the successful repair of an unconventional cement packer damaging the second casing in the eccentric annulus. The design, 4 ½” in 9 5/8” with limited cement. CannSeal’s CannSeal heater tool was used in order to increase the ep- technology achieved the objective of reducing the gas leak oxy materials cross linking, establishing a strong plug. to within acceptable limits, thereby facilitating develop- A total of three epoxy injections was completed (31,6L ment of an additional reservoir. ea.) throughout the job. The injections were placed in close
In order to unlock additional accumulation, the wellbore proximity, and the CannSeal heater tool was deployed to was sealed off and the A-annulus was ? lled with cement increase the strength of the plug material. This enabled it above the top of the additional reservoir. Two long forma- to withstand high delta pressure in an anticipated large tion, or reservoir sections, were then perforated below the open void in the event there was no cement. Orientation estimated Top of Cement (TOC) in the A-annulus. When of the tool was successful despite a low clearance, making production started, the A- and B-annuli developed gas in- the concept viable for larger casings in the future. ? ux issues. Conventional methods of sealing could not be The aim of lowering the gas leak rate was successfully used due to the risk of ? lling the reservoir with sealant achieved. A month after the treatment was completed through the perforated sections. the situation was reported to be similar, with the pressure
The cement below the estimated A-annulus TOC was build reduced to a minimum. of unknown quality and the 4 ½” tubing was placed in- CannSeal’s Chief Executive Of? cer, Bengt Gunnarsson, side the 9 5/8” casing. Perforating through a thick cement said CannSeal is a problem solver for operators who expe- sheet, while not damaging the outer casing on the low side, rience unexpected well integrity issues. “Without a suc- was vital to the project. CannSeal’s criteria was to remove cessful barrier repair, on this occasion it would not have or reduce the gas leak to within acceptable limits. been possible to develop this additional reservoir through
The CannSeal IntegritySeal was run on wireline to per- conventional methods. forate and inject epoxy in the cement above the top per- “Committed to innovation and global growth, we are foration interval. CannSeal’s high viscous sealant forms a proud to share success stories like this. Following the re- doughnut around the tubing in an open void, or ? lls large cent launch of our mobile mixer, we are now able to reach channels in a poor cement matrix. This process creates a more markets faster than ever before.” plug independent of annular condition. The launch of CannSeal’s new mobile mixer was a strate-
Cannseal’s delivery tool is ? tted with a g-sensor, which gic investment for the company. Facilitating the company’s has the ability to show the tools relative orientation. As a proprietary epoxy resin to be mixed on-site, the mobile result, eccentric centralizers were used to point the perfo- mixer opens up new markets independent of location as it ration gun in the desired direction. This allows selective removes constrictions associated with storage and curing.
November/December 2019 OFFSHORE ENGINEER 51