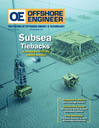
Page 22: of Offshore Engineer Magazine (Mar/Apr 2020)
Offshore Wind Outlook
Read this page in Pdf, Flash or Html5 edition of Mar/Apr 2020 Offshore Engineer Magazine
SUBSEA Tiebacks
Source: Lee Thomas, Intecsea
TESTING NEW
TECHNOLOGIES concept that could extend the distance of gas tie-backs to in excess of 150km up to 350km could take another step forward this year. The concept, driven by Lee Thomas, Lead Development
Engineer at Intecsea, would involve placing multiple, in-line piggable A separators along a long pipeline tieback system in order to remove liquids that condense from the gas during transportation (see OE: May/June 2019). Supported by small, single phase centrifugal pumps, larger pipeline diameters could be used to reduce back pressure – by some 50-180 bar.
Following modelling by Intecsea and the University of Strathclyde in Glasgow and six-inch scale model testing at Cran?eld University’s ?ow loop during 2019, Intecsea now hopes to build a pre-production hydrocarbon prototype of the pseudo dry gas (PDG) system concept.
PDG Unit in Testing: A scale model test of the pseudo dry gas
It will use a hydro-mag subsea pump from Norway’s FSubsea and a system has been put through its paces.
subsea control system. This would be tested at the new NEL facility just south of Glasgow in the UK with simulated hydrocarbons up to 120 bar.
This will verify modelling and the scale model testing already done through a joint industry project with the Oil & Gas Technology Center.
After that, Thomas says that the pre-production prototype would be installed on an onshore gas ?eld to run it for three-months for an endurance test. This latest testing is focused on building a consortium of partners in the technology and pursuing a number of funding avenues, which could be approved later this year. These steps would help take the technology to TRL5-6 by 2022, says Thomas.
The system could be used instead of subsea gas compression (or ?oating compression), which costs more and is based on adding energy to an energy insuf?cient ?ow system – based on industry project announcements subsea compression also has a high entry point in regards to gas ?eld size, currently running an average of 12.5 Tcf, he says. “The core problem with long distance deep-water gas tiebacks is a liquid (multiphase) problem, excessive pressure drop is a symptom of the problem, the further and deeper the tie- back the more excessive this symptom becomes generating highly negative secondary and tertiary order side effects, PDG focuses on addressing the problem rather than the symptoms,” says Thomas.
A speci?c project he’s assessed, under the work with the OGTC, is for a west of Shetland gas condensate tieback in the UK sector.
This would be a 200km, 2.5-6.5 Tcf project (?rst phase-full basin) covering stranded gas ?elds in 1700m water depth. It would need two pipelines, one larger for gas and a small one for liquid handling (which is eligible for composite materials) with four liquid removal units at stages along the pipe – i.e. about 30, 45, 75, and 90m along the pipe.
Modelling suggested it could add 10 and 6 years to plateau production, compared with a subsea compression solution at 32 and 80 bar respectively and offer 74% recovery, compared with 51% and 61%. CO2 emissions and economics were also assessed, both favorably.
Areas like the Mediterranean, where signi?cant deepwater gas ?elds have been discovered, East Africa and Trinidad, as well as
Australia, where there are pockets of gas in deep water to neighboring existing infrastructure (<350km) offer signi?cant potential for this technology, says Thomas, who was spoke to OE during this year’s Subsea Expo. and subsea connection systems. and umbilicals ?rm JDR, says, “We’re seeing big intertest in-
The vision for Aptara tree lead times is 9-11 months, says Ro- terest in optimizing functions in the umbilical, to make tie- main Chambault, Director Europe - Oil?eld Equipment at Bak- backs more cost effective.” er Hughes GE, with 12-14 months being the current schedule, JDR invested in a horizontal laying up machine in 2016, compared with 24 months in the past. The ?rm also has a stra- which means it’s been able to do more complex umbilicals tegic alliance with Microsoft Azure and C3.ai to bring arti?cial and cables, with cores mixing up steel tube and thermoplastic intelligence (AI) to bear. But, Chambault says commercial mod- hose, depending on operator requirements. els, such as incentivized contracts and closer working through That could be any mix of super duplex, to allow for faster alliances, will be what allows the industry to move forward. response time, thanks to its lower volumetric expansion or high chemical resistance, thermoplastic, ?ber, power of chem-
JDR ical hose, all in one system. This is useful for those wanting to
The focus on cost extends to components within the tie- connect into existing infrastructure or to add in water injec- back system. James Young, Chief Technology Of?cer at cables tion, he says. 22 OFFSHORE ENGINEER OEDIGITAL.COM