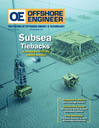
Page 41: of Offshore Engineer Magazine (Mar/Apr 2020)
Offshore Wind Outlook
Read this page in Pdf, Flash or Html5 edition of Mar/Apr 2020 Offshore Engineer Magazine
ROBOT REVOLUTION need someone on them once a year – or “NUI-1Y”, as Total’s
Total has been perusing developments in robotics that called it, providing “a new frontier for cost reduction”, accord- would mean routine inspection and maintenance could be ing to a 2019 OTC paper. Equinor and Saft have partnered done using robots, limiting even further how often humans with Total on the OGRIP (Offshore Ground Robotics Indus- would have to visit a plant. The French energy major has trial Pilot) robot project, which aims to develop the “world’s been working with German robotics ?rm Taurob (OE: Janu- ?rst Offshore Work Class Robot (OWCR)”. ary 2018), which won Total’s Autonomous Robot for Gas Others are following. Earlier this year, Aker BP formed and Oil Sites (Argos) challenge, partly sparked by the Elgin- a strategic partnership with Cognite, which it part owns,
Franklin gas leak in 2012, which could have been easier to to explore the potential of robotics in the offshore oil and deal with using robots on the platform (as it was too danger- gas platform. ous for humans to board). New technologies like this are enabling operators to think
After winning the competition in 2017, Taurob’s further differently, from control systems to robots and drones, which developed the robot and undertook onshore trials at Shetland have made big in-roads in recent years for inspection work,
Gas Plant last year (2019). Earlier this year, Total was due to albeit with a human operator nearby – but that could change. take over ownership of two versions of these robots with a Data monitoring, remote operations, telecommunications – view to trailing them on the Culzean platform in the North the advent of 4G LTE for example – and robotics are now on
Sea and then a NUI. The end goal is for installations that only the scene and enabling things to be done differently.
Upstream, without a crew here are also concepts for unmanned ?oating systems. Various unmanned production buoy concepts have been covered in these pages numerous times before. They’ve not yet taken off, but some are still hopeful (see panel).
Now, engineering ?rms including TechnipFMC and Aker Solutions are offering new solutions.
T A ?oating UPP is one of the concepts being considered for Peon. The ?eld was discovered in 2005 and has a thin gas column over a large area. In 2012, because of the ?eld’s properties, combined with being a long distance to possible host platforms and there being a lack of capacity in the gas transport system, it wasn’t deemed economically viable. Now,
Equinor has said it’s working with Gassco and Neptune Energy to investigate the possibilities of phasing Peon in, into either the Kollsnes processing plant onshore, or to Gjoa ?eld facilities, about 60 km south of Peon, via a ?oating UPP.
TechnipFMC and its engineering subsidiary Genesis has focused on a minimal unmanned ?oating substructure for applications including platforms for production, compression, power and wind turbines, using a spar concept. It also looked at alternatives to a spar, such as an extended draft platform (EDP) buoy, which could be used for applications including supporting a low-cost subsea development. Its columns and pontoon are raised, which allows for equipment to be installed in the deck box when it is at ground level or ?oating in a collapsed con?guration. The shape of the deck box also provides suf?cient area for processing, power, communications, instrumentation, and material-handling equipment.
Without people onboard, you can simplify design of the substructure, as the stairs and elevators normally needed to allow people to access the inside of the substructure can be replaced with ladders and ropes that require less space, according to another OTC 2019 SPE paper.
Aker Solutions is also looking at unmanned FPSOs, with remote operation, control and surveillance. That means eliminating quite a lot of functionality, says Nyborg: “no living quarters and preferably also without a helideck, but depends on the location.” It also means systems that can sustain shut-in well pressure and live without ?aring, as well as being all electric with high reliability equipment. A change in maintenance methodology would also be useful – having self-diagnostic plug and play systems where an entire unit is just switched out instead of needing complex operations, like today’s cars, minimising offshore man-hours and not requiring specialists.
Today, the goal is to design facilities that reduce maintenance and start to require people onboard just 1-2 times a year, says Nyborg. That’s a steppingstone for more self-diagnostics and calibration, as well as use of robots, which could also reduce the number of people needed on facilities, from say 80 to just 15. Longer term, could truly unmanned be achievable? march/april 2020 OFFSHORE ENGINEER 41