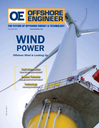
Page 15: of Offshore Engineer Magazine (May/Jun 2020)
Read this page in Pdf, Flash or Html5 edition of May/Jun 2020 Offshore Engineer Magazine
Both images: BPT’s power and control buoy design, confgured to support long-range and challenging tiebacks by providing utilities at the wellsite and removing the need for an umbilical from the host facility. uoyant Production Technologies ing at the University of Edinburgh’s FloWave (BPT), a subsidiary of Crondall Energy Ocean Energy Research Facility. SBT also has
Consultants, is promoting a foating a storage tank concept, that could be deployed
B
NUI for low life-cycle cost developments of with the buoy, so that applications from power marginal felds, which are unsuitable as sub- and communications through to production sea tiebacks due to distance, power and host and storage systems could be supplied. facilities requirements, or to enable the devel- Malcolm Bowie, consultant, at SBT Energy, opment of long-range or challenging tiebacks, says an example use of SBT’s catenary moored e.g. providing the utilities at the wellsite. Da- system could be on a two-well 10-15,000 barrel vid Steed, general manager at BPT, told Subsea a day feld, which would require a 24m-diame-
Expo in Aberdeen that the frm’s single column ter, 60m-tall part submerged buoy, comprising foating facility design, suitable for harsh envi- 2000-tonne of structural steel. For a two-year ronments, could support a 20,000 b/d subsea feld life tieback, that would be and economic tieback with power – which could be for sub- way to remove the pain of platform modifca- sea pumps, or electric downhole pumps, etc. - tion and engineering, says Bowie. For just a or provide full production support to a 30,000 control buoy, the system would be about half b/d feld. The concept, which has Lloyds the size. It could also be deployed with wind
Register Approval in Principal, would have energy or battery back-up he says, depending remote operations and monitoring and peri- on system and functionality requirements. odic maintenance via walk-to-work. The frm A key design challenge SBT has focused on has worked on a non-feld specifc pre-FEED is motion, says Bowie, using distributed ballast study under the OGTC’s Facility of the Future weight at the bottom of the buoy, to reduce the programme to demonstrate what is feasible. It natural period of the buoy; so pitch and roll is looked at a 20,000 bo/d oil development with as small as possible by adding mass, not weight. 25,000 b/d of produced water and 400 scf/bbl The wave tank testing, done last year, saw 7-de- in 150m water depth. Steed says opex for this, gree pitch, in the most extreme conditions and using their NUI, would be $7/bbl, at $9/bl ca- Bowie says they think they can get less than that. pex, based on a six month visit frequency and “A [normal] FPSO rolls up to 20-25 degrees in recovering 25 million barrels over 10 years. even operational sea states,” he says. “We’re now “The challenge for us is that operators think engaging with operators and doing a study for in a certain way,” says Steed. “There are subsea operator for a feld life extension solution. It can people or foating people. It’s diffcult to get plug into existing infrastructure and continue them to think about the whole infrastructure production when existing facilities are no lon- and think outside the box.” Dealing with pro- ger economic to run or be used as an early pro- duced gas is the biggest challenge, but there are duction system to better understand a reservoir. options, like gas to wire and integration with “The sweet spot is as a control buoy for oil and offshore wind, he says, which also aids emissions gas tiebacks, where operators would otherwise reduction. The hull design could also be used for need modifcation to platform which could be foating sub stations for offshore wind, he adds. painful. It could also extend to water injection.”
Another idea the frm is working is subsea gas
SBT Energy storage, to smooth out demand supply cycles
SBT Energy, which used to be known when gas is used as part of the system. It could as Offshore Production Buoy (OE: August also be converted to electricity and exported, 2017), also has a production buoy design i.e. gas-to-wire, says Bowie, or, if deployed with which it recently put through wave tank test- a wind turbine, used to create hydrogen.
MAY/JUNE 2020 OFFSHORE ENGINEER 15