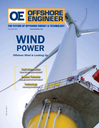
Page 18: of Offshore Engineer Magazine (May/Jun 2020)
Read this page in Pdf, Flash or Html5 edition of May/Jun 2020 Offshore Engineer Magazine
SUBSEA SUBSEA TIEBACKS value chain and developing the capability of identifying where have re-designed the fow path of our pipes, which means they those small changes can be most effectively made. require fewer valves and smaller valve blocks. Fewer compo-
At Baker Hughes, we believe there are signifcant volumes of nents means lower costs, and less risk.
contingent resources that can be made economic by adopting a new approach to product development and supply (Rystad Manufacturing and digital data indicates this volume could be as much as 16 billion bar- With new designs and material specifcations in place, rels oil equivalent). Our research suggests that the economic manufacturing the product becomes easier and quicker – and development point of subsea projects can be reduced by an the cost savings start to ripple out through the value chain. average of 30%. Logistics and transport consume less budget as smaller and
Nonetheless, these small changes do require a big shift in lighter pipe can be transported by smaller and lighter vessels. mindset. It requires meaningful partnerships between suppli- Deployment and installation are quicker and easier, which ers and operators at a much earlier stage in the design and then makes it possible to identify and address any quality is- development process. Digital tools, planning and risk man- sues that arise much earlier in the process. agement are central to that process. To reach the economic target, it is imperative to design fexibility and modularity into subsea technology.
The potential of tie-back capabilities
Developments in tie-back technology are just one illustra- tion of the value that can be created. The industry has come a long way since tie-back connections of 2-3 km were consid- ered extraordinary and has continued to push the boundar- ies of technical capability to tie back felds. From fber optic cabling to vessel size, all have expanded aggressively – as have the number of potential reservoirs that could be exploited in a fnancially viable way.
Today, we are looking at tie-back distances of more than 100 km. Fields in the Gulf of Mexico that have been produc- ing since the 1970s and have reached what was considered to be end-of-life, can now realistically increase their capacity by using tie-back technology to keep pipelines running.
By having advanced technology in terms of tie-back capabil- ities, another shift is underway as frms like Baker Hughes en- deavour to extract redundant costs through improved design.
As with the components of our Aptara TOTEX-lite subsea system, we have been re-thinking our tie-back technologies to make them modular, structured, compact and more respon- sive to changing conditions across the life of feld.
That means looking at materials in a new way, for example, by bringing in composite materials from the aerospace indus- try to create pipes that are vastly lighter than traditional prod- ucts. That can achieve signifcant cost savings: there may be an initial front-loaded expenditure, but eventually, fewer ma- terials means fewer costs and less impact on the environment.
Although making things less expensive and lighter weight is essential, re-thinking design goes beyond that. The funda- mental design can present further opportunities to eliminate costs that have traditionally been overlooked. In this case, we 18 OFFSHORE ENGINEER OEDIGITAL.COM