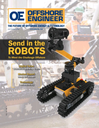
Page 18: of Offshore Engineer Magazine (Jul/Aug 2020)
Read this page in Pdf, Flash or Html5 edition of Jul/Aug 2020 Offshore Engineer Magazine
MAINTENANCE UPDATE Bearings $375 and $875 billion annually on a global basis. (PVDF). Like 316 grade bearings, these should only be used
The overall effect of corrosion is inherently damaging to in low load and low precision applications.
offshore structures, as it weakens the structural integrity of Another level of armor against corrosion is a protective coat- the facility itself. What’s more, it’s impossible to ignore the ing. Chromium and nickel plating offer good corrosion re- signi?cance of corrosion costs. However, corrosion resistance sistance in highly corrosive environments. However, coatings must be considered alongside other operating requirements, will eventually separate from the bearing and need continual such as bearing longevity and load. After all, many external maintenance. For this reason, coatings aren’t the most practi- factors can prematurely affect a component’s operating life. cal option for offshore environments. To protect machinery
For example, a marine riser tension system is required to and equipment from failure, internal components must be operate with precision but must also operate in unforgiv- high quality and preferably, low maintenance.
ing conditions, which threaten contamination. Due to the extreme environment of oil and gas rigs, corrosion-resistant MATCH YOUR LUBRICANT TO THE APPLICATION bearings would be recommended. If a design engineer were Surface roughness and lubrication affect whether surface to opt for a highly corrosion resistant bearing fabricated from distress will occur, so opting for the correct lubricant matters. polyether ether ketone (PEEK), this would stop the corrosion A proper lubricant will reduce friction between the internal in its tracks. Still, the precision of the machine would be com- sliding surfaces of the bearing’s components, dissipate heat promised. In this scenario opting for a high precision stainless and inhibit corrosion on the balls and raceways. steel bearing with superior roundness, while allowing some Super?cial corrosion may occur on the outside of the bear- super?cial corrosion may be preferable. ing; however, it should not be allowed to occur on the inside.
In the ?ght against corrosion, ensuring the right equipment Opting for a sealed bearing with waterproof greases that con- is selected is the ?rst step — and this is imperative for both tain corrosion inhibitors, is advised. These lubricants protect large-scale machinery and small components, such as bear- the internal surfaces of the bearing and can be matched to the ings. So, what are the key bearing design considerations for speci?c offshore application environment. Full ceramic bear- offshore environments? ings are mostly speci?ed without lubrication but can be lubri- cated with waterproof grease for extended life.
CHOOSE YOUR MATERIAL WITH CARE In harsh environments, contamination protection is of utmost
For offshore oil and gas facilities, stainless steel is the most obvi- importance, so opting for a contact seal is favorable to ensure ous bearing material choice. It offers corrosion resistance, but also contaminants do not enter the bearing. For equipment that may bene?ts from other advantageous properties such as durability be exposed to moisture, a contact seal will also offer increased and heat resistance. The latter is particularly important, as rates water resistance. This will stop grease washing out of the bearing, of corrosion can increase in environments with pressure and heat. allowing it to do its job in lubricating and protecting the internal
For instance, 440 grade stainless steel is known for its resis- surfaces of the bearing. An alternative option is a metal shield, tance to damp environments. However, this grade has poor re- but this offers greatly reduced protection against moisture.
sistance to saltwater and many stronger chemicals. Consequent- ly, for harsh offshore environments, 316 stainless steel may be THE ENEMY OR A HARMLESS DISTRACTION?
considered. However, as 316 stainless steel cannot be thermally Corrosion control is just one performance requirement, hardened, these bearings are only suitable for low load and low- which doesn’t necessarily equate to poor performance or af- speed applications. They should only be used in marine applica- fect the bearing’s internal rollability. Downtime is one of the tions above the waterline, or in ?owing, oxygenated water. biggest challenges for offshore facilities, so a holistic design
An alternative material option is ceramic. Full ceramic bear- approach must be followed to increase equipment uptime and ings made from zirconia or silicon nitride with PEEK cages minimize maintenance. can offer even higher levels of corrosion resistance and are of- Luckily, offshore facility managers can assess the operational ten used fully submerged. environment, required longevity and loads that will be ap-
Similarly, plastic bearings, with 316 stainless steel or plied to the bearing and can weigh up whether opting for glass balls, provide very good resistance to corrosion. These a corrosion control design feature will be the most cost ef- are often made from acetal resin (POM) but other materi- fective, increase the bearing’s lifespan and elevate a machine’s als are available for stronger acids and alkalis such as PEEK, performance. After all, the best bearing may not be the one polytetra?uoroethylene (PTFE) and polyvinylidene ?uoride that remains looking aesthetically pleasing for the longest.
18 OFFSHORE ENGINEER OEDIGITAL.COM