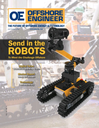
Page 29: of Offshore Engineer Magazine (Jul/Aug 2020)
Read this page in Pdf, Flash or Html5 edition of Jul/Aug 2020 Offshore Engineer Magazine
Meet Total’s “S
TEVIE THE ROBOT”
Total has been working on robotics for some years now, having launched the Argos challenge in 2013 and now getting ready to put the Taurob designed Stevie robot through its paces in a trial at Shetland Gas Plant.
We spoke with Kris Kydd, Head of Robotics, at Total E&P UK.
that can be run from the digital twin system. This is where
What have been the main lessons learned to users can indicate the inspection points of interest and this date around enabling these systems to oper- is then translated into robotic commands for the robot. It is ate in an offshore environment?
Total believes that robots have a huge amount to offer to this digital architecture that will allow us to extract maximum our industry. We are pioneering their use on oil and gas sites, value from robots. Total now appreciates that using a robot to and the last seven years have seen progress, and lots of lessons support operations does not mean keeping the robot on site. learned! Robots offer immediate advantages such as increased What is essential, however, is learning to make the best use of safety and ef?ciency. In the long-term, they offer us new ways it; recognizing the changes to operations that robotics imply and updating operating philosophies accordingly.
of working and are limited only by our imagination.
A major lesson learned is that the performance of any au-
Has anything changed in that period that tonomous wireless robot is only as good as the quality of its would have been of benefit to the teams surrounding digital architecture. We have taken this to heart back in 2013? and developed a digital architecture that is device agnostic and
Machine learning has taken off in a big way since Total designed to be used with any robot system or mobile device. launched the ARGOS challenge. If machine learning had
In the early stages, we had all the autonomous processing per- formed on board the robots. This led to issues with the battery been as prevalent then as it is now, then we would have in- power running down too quickly; it also limited storage space cluded it from the beginning. If we’d had a digital architecture and processing power on the robot which we’ve upgraded by to interface with the robot, then we also could have tested the end-to-end functionalities. moving non-critical processing to the cloud. A reliable com-
A digital architecture means the robot gets all the data it re- munications network is also essential. Available bandwidth quires to complete a mission from a digital twin, which is our and latency completely dictate what you can do.
We have also developed robot mission planning capabilities single source of truth and contains the latest site data. Then,
JULY/AUGUST 2020 OFFSHORE ENGINEER 29