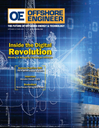
Page 30: of Offshore Engineer Magazine (Sep/Oct 2020)
Read this page in Pdf, Flash or Html5 edition of Sep/Oct 2020 Offshore Engineer Magazine
FEATURE SUBSEA PIPELINE
Targeting HPHT repairs coiled tubing-based system, using hot tap technology to access
Luckily, it doesn’t happen too often, deepwater pipelines the pipe and then a special design clamp to close the hot-tap being less prone to external damage. They’ve had one call hole once the pipe has been unblocked of wax or hydrates, etc. out for a clamp repair in 2010 and nothing since, so focus is on ensuring the equipment is well maintained, says Rebello. Internal repair options
SES is also looking at new technologies, specifcally around Another research project is called Irep. It’s a remote-controlled repairing high-pressure high-temperature (HPHT) pipelines internal repair system. It’s like a pipeline inspection tool that is and the use of coiled tubing to unblock paraffn and hydrate pumped down the pipeline to where a crack or pinhole leak is blocked pipelines. (located by a magnetic sensor mounted on an ROV standing-
The RUPE and DW RUPE systems are all ANSI class 900 by near the damaged area). Once in position, it releases a sleeve and 1500, respectively, and use elastomer seals. For HPHT that is remotely activated using a ratchet design to create a seal use, SES has assessed other seal materials and came up with around the full internal circumference of the pipe. Because it graphite radial seal rings that have now been tested to 22,500 does the repair from the inside, the lifting tools aren’t required, psi. For unblocking deepwater pipelines, they’re working on a vastly reducing logistics and cost, says Rebello. Another future
BARCODES TO DRIVE
DOWN PIPELINE
INSPECTION COSTS
Figure 1: Illustration of subsea pipeline inspection using barcode tags integrated into a pipeline and an ROV
Source: Screenshot from an iXblue, Vallourec, Forssea Robotic video
Three French companies are working on a Vehicles (AUVs) or Remotely Operated Vehicles need for acoustic positioning systems and pipeline inspection solution that combines (ROVs). The subsea vehicles then collect the costly mother vessels.
ROVs and the use of visual markers - barcodes required information – such as a pipeline’s Per the project participants, the markers are - directly integrated on subsea pipelines. general aspect and route, anode consumption, resistant to marine growth and erosion. Thus
The solution, being developed by tubular free span, burial, and crossing areas – using they will remain visible to divers and subsea solutions frm Vallourec, smart robotics and observation sensors. drones throughout the project’s lifespan, visual positioning start-up Forssea Robotic, The project relies on barcodes placed “This technology had already proven itself and subsea positioning and inertial navigation on installed pipes, resulting in many on large structures in the feld,” said Jean- frm iXblue, promises to drive down the costs passive positioning references logged with Guillaume Besse, Vallourec R&D project of subsea pipeline inspections. their own coordinates during the laying leader. “Back in January of this year, we did
According to the companies involved, operation, which will remain accessible a frst sea trial on much smaller surfaces the solution would remove the need for throughout the feld’s life. – down to pipes of 6” in diameter – in the surface vessels, traditionally used in pipeline These markers would be used as navigation South of France. The tests were a success, inspection projects. support for subsea drones equipped with proving that these markers, combined with
Usually, surface vessels with acoustic Forssea cameras and iXblue’s inertial iXblue’s and Forssea’s expertise, can be used positioning are used to monitor the navigation systems that relay the pipelines’ to provide accurate subsea positioning without deployment of Autonomous Underwater locations to the operators, thus removing the the need for acoustic systems.” 30 OFFSHORE ENGINEER OEDIGITAL.COM