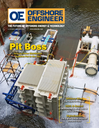
Page 33: of Offshore Engineer Magazine (Nov/Dec 2020)
Read this page in Pdf, Flash or Html5 edition of Nov/Dec 2020 Offshore Engineer Magazine
n 2017, the Brazil National Petroleum Agency (ANP) is- sued a failure mode alert: stress corrosion cracking (SCC-
CO2) triggered by the presence of CO2 in high-pressure
I pre-salt conditions had been identi?ed as the cause of bro- ken tensile armor wires on a certain ?exible pipe installation.
Relatively common in other applications where carbon steel is subject to high CO2 concentrations, this failure mode was unknown in ?exible pipe – and it presented a major challenge for operators in Brazil’s extensive pre-salt ?elds.
Flexible pipes have played an important role in Brazil’s his- tory of oil production.
No other oil province in the world has applied ?exible pipes so intensively as the Campos Basin, for example, where ap- proximately 2,223 km of risers and ?owlines have been in- stalled to connect giant ?elds including Marlim, Albacora and Roncador, in water depths that range from 1,500m to 2,000m. It’s no exaggeration to say that ?exible piping has been crucial to the development of Campos and other basins as viable production sites.
FLEXIBLE ADVANTAGES
Of course, ?exible piping is not exclusive to Brazil. Its wide- spread deployment is down to the many advantages it offers to so many operators. With concentric and unbonded layers, each of which contributes to the mechanical strength and chemical resistance needed to withstand deep-water conditions, ?ex- ible pipes were designed to ensure collapse resistance, internal pressure capacity, bending stiffness and axial-load capacity – among numerous other advantages to deep-water operations.
In addition, this unique design gave operators several logis- tical advantages. Flexible pipes can be transported on smaller, nimbler, and more cost-effective vessels. Manufacture does not require quality-sensitive offshore processes such as weld- ing or ?eld-joint coatings – both of which have, historically, raised concerns about operational integrity.
As the name suggests, they also give operators the luxury of ?exibility and enable them to make subtle but important changes at later stages of a project without incurring severe cost penalties.
Once in production, ?exible piping gave operators the op- tion of moving subsea lines and re-positioning pipes in re- sponse to production needs, or to postpone the exact location of production-well placement decision. As operators started production and built knowledge of reservoir behavior, that ?exibility allowed them to optimize both output and ?eld life.
That ability to be easily recovered, inspected, repaired, re-laid and connected at new sites was key: ?exibles proved themselves to be the best way of reducing time to ?rst oil by enabling feasible production in short timeframes, even before reservoir de-limitation and subsea layout consolidation. They
November/December 2020 OFFSHORE ENGINEER 33