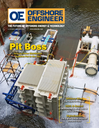
Page 37: of Offshore Engineer Magazine (Nov/Dec 2020)
Read this page in Pdf, Flash or Html5 edition of Nov/Dec 2020 Offshore Engineer Magazine
PRODUCTS SUBSEA TECH
WellSense save up to £150,000 (around $200,000)
Collared Monopiles
RWE will deploy special collars around per offshore wind turbine per year, ORE the monopile foundations at the seabed Catapult said.
level at its Kaskasi offshore wind farm, in
Floating buoy for what has been described as “the ?rst time subsea power ever in the renewables industry.”
Ocean energy technology developer
The ‘collared monopile’ technology
Ocean Power Technologies (OPT) has will provide additional support for lat- received a DeepStar project award to eral loading, increase the bearing capac- ity and improve the structural integrity study the use of its PB3 PowerBuoy of the entire foundation – especially in to provide remotely controllable zero- carbon power for deepwater subsea oil dif?cult ground.
DEME Offshore will transport and production applications.
OPT’s moored ?oating buoys - such install the new foundation technology at the Kaskasi wind farm in the German as OPT PB3 PowerBuoy - harvest wave
North Sea. Also, Kaskasi will be the ?rst energy and convert it to electricity.
The project will explore using OPT’s commercial offshore wind farm in the world to use an improved installation PB3 PowerBuoy and a subsea battery to reduce the cost and carbon emissions method to drive all monopile founda- tions to target penetration. The vibro associated with conventional means of pile driving technique will reduce both powering and controlling subsea oil and gas production equipment. The study installation time as well as noise emis- will consider water depths of 1000, sions for marine life.” 2000, and 3000 meters.
The wave-energy buoy, i.e., power iFROG
An amphibious robot called iFROG source, can be placed closer to the pro- capable of working in teams to clean duction site reducing the cost of a subsea and inspect monopiles above water umbilical. Coupled with a modular sub- level and up to 60 meters below (~6 sea battery (energy storage in the 100- bar), has recently completed trials at 500 kWh range) it provides suf?cient the Offshore Renewable Energy (ORE) power to operate electric trees, SCMs,
Catapult’s National Renewable Energy and HPUs. This enables decarbonization and autonomous, remotely controlled,
Centre in Blyth.
Teams of iFROG robots will be able all-electric subsea production.
to clean corrosion and biofouling from
Terminator monopiles, before inspecting the surfac- Baker Hughes has recently launched es and conducting pre-emptive checks its vessel-deployed subsea wellhead cut- of weld integrity.
During the ?nal trials, two robots ting system Terminator.
Using a ?rst-of-its-kind mechanical demonstrated how they can work togeth- wellhead removal method, the Termina- er in a team above and below the water- line. The ?rst robot performed corrosion tor system cut a subsea wellhead from mapping and water-jet cleaning of the an abandoned exploration well owned monopile. The second robot inspected by Wintershall DEA in Norway.
Baker Hughes worked with Winter- weld lines to assess integrity and ?ag po- shall DEA to cut the subsea wellhead tential defects, ORE Catapult added.
from an abandoned exploration well in
By increasing the frequency and qual- ity of subsea inspections, iFROG can 360-meter water depth in only 35 min-
Baker Hughes
NOVEMBER/DECEMBER 2020 OFFSHORE ENGINEER 37