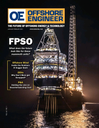
Page 27: of Offshore Engineer Magazine (Jan/Feb 2021)
Floating Production Outlook
Read this page in Pdf, Flash or Html5 edition of Jan/Feb 2021 Offshore Engineer Magazine
THE HOLE
Sitting at 49% of the total cost of decommissioning, wells plugging and abandonment (P&A) has long been high on the hit-list on the decommissioning cost reduction agenda. It’s a task that has no returns on the cost to do it, and activity is increasing. Elaine Maslin looks at some of the latest technologies aiming to reduce that cost. ell decommissioning activity outstripped ex- dustry, says Louden. The company uses alloys, bismuth, and ploration, appraisal, and development activ- non-bismuth based, that are melted in the well using a ther- ity combined on the UK Continental Shelf mite heating system to create a barrier with a metallurgical for the fourth year running, Kenny McAllis- bond with the steel or expands against the in-situ cement and/
W ter, section chair of the Society of Petroleum Engineers (SPE) or geological rock to create a barrier. in Aberdeen pointed out to the Offshore Decommissioning The metallurgical bonding between the steel and alloy cre-
Conference, held online late November, citing data from Oil ates a kind of sub-aquatic soldering, says Louden, so there’s & Gas UK’s latest Decommissioning Insight Report. higher shear bond strength than simply relying on friction
As activity rises, technology companies are also gaining to create a tight seal. That also means less alloy is needed in more traction with their concepts for alternative barriers to shorter lengths than the unbonded bismuth-based seal alter- permanently seal wells. One of those is Aberdeen based isol8. natives, he says. The entire system, called Fusion, is adapt-
Last year, the company, set up in 2017, quali?ed its metal- able to meet well-speci?c conditions. The same 3 ½ inch tool lurgically bonded-alloy barrier technology in an offshore tri- string size can be used in a wide variety of well geometries and al. Isol8 now has 7-10 on and offshore projects lined up for can be deployed through tubing on wireline or slickline. 2021. Others, including BiSN and Norway’s WellStrøm, are Last September, a 5-inch Fusion barrier was quali?ed at also making signi?cant inroads. isol8’s facility in the US. The following month, a Fusion bar- rier was deployed down to 10,765ft on a 3 ½ inch tool string in a 110°C 30-degree deviated well for Repsol Sinopec Re-
Isol8’ing wells
The drive to create new barriers materials is largely to re- sources’ UK on their Fulmar ?eld, – its ?rst offshore trial. duce reliance on rigs for offshore operations. “The big cost There, 1m of alloy above the thermite heater was deployed on saving for well P&A is avoiding the need to pull tubulars,” e-line and, once it was set, the world’s ?rst bonded-alloy bar- said Andrew Louden, founder of iSol8. “The holy grail is for rier was tested with pressure from above and below. phase one zonal isolation, phase two intermediate isolation, The bridge linked North Sea Fulmar Alpha platforms are and the environmental cap to be deployed without the need about 217 miles east of Dundee and were installed in 1981 for a rig.” This is particularly valuable for subsea wells which with ?rst oil in 1982. can cost $10 million per well, he says. isol8 is now preparing for 7-10 projects this year with mul-
Isol8’s goal is to create a metallurgical bond with steel with tiple operators and for a range of different well geometry ap- the highest sheer bond strength and life expectancy in the in- plications. The next will be onshore; again a 3 ½ inch tool january/february 2021 OFFSHORE ENGINEER 27