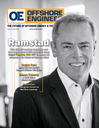
Page 39: of Offshore Engineer Magazine (Mar/Apr 2021)
Offshore Wind Outlook
Read this page in Pdf, Flash or Html5 edition of Mar/Apr 2021 Offshore Engineer Magazine
“You also need a large stable platform to be more robust And then, of course, in between two monopiles, you do have in relation to your harsh alignment out in the North Sea; the transition piece, and we decided to carry the transition pieces larger, the better,” said Ramstad. “So, we started off with some on the SQ back. That’s normally where you have a big hotel iterations and it grew and grew and grew, because the frst and section on the vessel.” the second iterations were too small, and eventually ended up With the main deck being prime real estate for effcient at the sizes we are at now. foundation handling, the decision was taken to place the hotel
Next up was designing a cargo handling system to effcient- portion of the ship underneath, allowing for much freedom in ly move and handle the massive piece of unique and valuable the placing of other valuable bits of equipment including the cargo … while buffeted by the notoriously rough North Sea. 900-ton piling hammer. “The piling hammer is a big beast,” “We said: ‘In order to mechanize and automate the process said Torstad, and that sits on the forecastle deck along with of installation, which is actually a serial production or repeti- the transition pieces. tive process, you need to handle things in parallel. You need
WHAT’S NEXT?
to not do everything in sequence. You need to also get rid of the people who are exposed on the main deck doing manual While the original Alfa Lift is yet to be delivered, thoughts operations,” said Ramstad. have already turned to Alfa Lift 2, which is currently in basic
In the fnal concept they placed a crane upfront on the vessel design. “We have made certain modifcations, essentially in to free up the space on the main deck, and created a mecha- relation to an even longer crane boom,” said Ramstad. “This nized deck transportation system to bring the foundation isn’t because of heavier foundations; we are well-covered with components up front towards the crane. Since the crane did what we have on Alfa Lift 1 in that respect. But, if the founda- not need to cover the entire main deck, it offers a shorter, more tions grow higher or longer, for instance, we see jackets stand- robust crane boom … and ultimately a cheaper crane, too. ing on the vessel’s deck soon becoming the limiting factor, in “With this deck transportation system, we can then feed terms of crane height or hook height.” So the team is looking the crane in the upending position, bringing them from the at a bigger crane with a longer crane boom.
horizontal to the vertical in an effcient way,” said Ramstad. “So, probably going from 3,000 tons to 5,000 tons,” said “And while installing one monopile, we prepare for the next. Ramstad. And with a bigger crane comes a slightly longer ship to ensure stability during sailing and install. “For most people it would look identical. It’s not that big a difference.”
OHT is currently building the Alfa Lift, an Ulstein-
While OHT has invested much time and resources to race designed offshore wind foundation installation vessel, and ahead in the offshore wind turbine installation game, Rams- has secured a contract for work on Dogger Bank phases tad said the trigger for further investment is up to the clients
A&B. Being built by China Merchants Heavy Industry (CMHI) shipyard in Jiangsu, China, the 51,087-dwt Alfa in the form of a contractual commitment. “We have invested
Lift will transport the monopile foundations and transition close to $600 million on speculation in Alfa Lift and jacket pieces to the offshore site and install them in water depths vessels and the organization. Now it’s the client’s turn to com- up to 35m, using the vessel’s 3,000-ton crane, mission mit. We are more than willing to push the button for Alfa Lift equipment and a 10,000+ m²’ ‘smart deck’, capable of carrying and installing up to 14 XL monopiles per voyage 2 or more jack-up vessels, and we have options for three more and will be able to fully submerge the main deck to a jack-up vessels as well. But we’re not doing it on speculation.” depth of 14.66m. The foundations will be amongst the “Now clients need to commit to us before we push the but- largest ever used for offshore wind and are expected to ton. And, I’m happy to note that several clients and are wak- be installed at Dogger Bank A between 2022 and 2023. ing up to that different dynamic in the market, because what
Specialist equipment suppliers for the vessel include the likes of Liebherr, MacGregor, MAN Energy Solutions, and they see is this bottleneck from ‘24 onwards. More and more
Kongsberg Maritime.
clients [are] coming to us, and probably to our competitors, to secure vessel capacity early. This is now close to early enough
Alfa Lift Dimensions
Length, o.a. 216.3 m Propulsion thrusters 3 x 5,500 kW for having enough lead time to actually order and construct
Length, bpp 204.3 m Retractable thruster 1 x 3,000 kW
Beam (molded) 56 m Tunnel thrusters (fwd) 3 x 3,000 kW a vessel. Whereas before, the lead times for contracts were
Depth (main deck) 12.6 m Positioning system DP 2 shorter than the time it takes to build a vessel. But now, it
Draft (design) 8 m Class DNV-GL
Draft (submerged max.) 27.6 m Deck strength 30 t/m2 looks like we are approaching a crossing point or even longer
Service speed 13 knots Complement 100 persons lead times for contracts. And therefore, we can sign a commit-
Installed power 4 x 6,875 kW ment for a vessel, push the button with the shipbuilder, get the vessel delivered in time, and perform the project.” march/April 2021 OFFSHORE ENGINEER 39