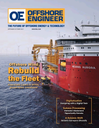
Page 38: of Offshore Engineer Magazine (Sep/Oct 2021)
Digital Transformation
Read this page in Pdf, Flash or Html5 edition of Sep/Oct 2021 Offshore Engineer Magazine
FEATURE SUBSEA PROCESSING could be captured “at source” and then reinjected locally, he instead of topside compressors, power consumption is reduced says, reducing the power needed for reinjection but also re- by up to 20% compared with topside compressors, he says. ducing the size of the production fowline and the amount of Overall, a 12% reduction in CO per barrel could be 2 topside equipment needed to condition the gas. reached, he said.
This is something Aker Solutions is working on, says Bar- As part of this work, Petrobras is also testing in a real feld ras, with qualifcation of gas separation membranes for subsea application a subsea variable speed drive (SVSD) for a 6MW carbon capture from natural gas ongoing. subsea motor, for applications where subsea power might
In Brazil, Petrobras, together with Libra Consortium part- come from a different platform to the one the oil is being ners, is also looking at high CO concentration gas removal produced to or longer tiebacks, says Koelln. 2 and injection at the seabed at ultra-deepwater high pressure, Moving the VSDs subsea would mean a 35-50% reduction high gas oil ratio (GOR) oilfelds with high (e.g. over 20- in weight and footprint of the HISEP topside module.
30%) CO content, Herbert Prince Koelln, Subsea Engineer “We have many reservoirs that may apply this technology in 2 at Petrobras told UTC in his presentation made with co- the future,” Koelln told UTC, but acknowledges many challeng- authors Ana Margarida de Oliveira, Fabio Menezes Passarelli es, not least in control and fuid dynamics and power control for and Marcello Augustus Ramos Roberto. load sharing and transient control, but also subsea cooling and
This would be possible through HISEP, Petrobras’ patented wax control, high pressures, and wide temperature ranges. high-pressure separation technology, currently in the qualif- cation stage.
Subhead Subsea seawater injection
The wellstream would frst pass through, initially, gravity-
Subsea water injection could also help reduce CO emis- 2 based separators, with dense gas being split off to two 6MW sions, says OneSubsea’s Lindøen-Kjellnes. OneSubsea com- pumps in series to be reinjected into the reservoir in a water- pared topside and subsea seawater treatment and injection alternating-gas loop, and the oil transported topside with a systems and found that in a base case 400 m deep feld, on a much reduced GOR. 30 km stepout, choosing a subsea system over a topside one
The idea is to help dealing with gas containing high CO could save about 70,000 tonnes of CO over the life of the 2 2 content at the seabed and debottleneck surface facilities, feld; equivalent to 11.3% reduction potential. which otherwise need signifcant ancillary equipment to han-
On a cost basis, topside equipment was thought to be less dle huge volumes of gas.
costly than subsea, but once installation and modifcation
By transferring part of the process (and in the future possibly costs were taken into account, the two options came close to- removing the entire process) from the topside to subsea, with gether. Subsea equipment also requires a lot less maintenance only single-phase pumps required subsea for the reinjection, and attention during operations, he says, saving costs.
MAN Energy Solutions has been commissioned to supply fve subsea compression units for the
Chevron-operated Jansz-Io
Compression (J-IC) Project.
MAN Energy Solutions provided the compression units for Equinor’s Asgard subsea compression project, delivered by Aker Solutions.
MAN Energy Solutions 38 OFFSHORE ENGINEER OEDIGITAL.COM