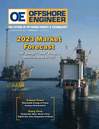
Page 55: of Offshore Engineer Magazine (Nov/Dec 2022)
Read this page in Pdf, Flash or Html5 edition of Nov/Dec 2022 Offshore Engineer Magazine
TECH FILE ROBOTICS grees of movement (via an IMU and GNSS), including up search facility in Cowes on the Isle of Wight, using real to 3m signi?cant wave height. The Neptune system uses vessel motion data as input. Andreas says a vessel-based dual, high speed CAN networks for rapid data transfer be- trial of this system was planned before the end of 2022. tween sensors, controllers and actuators. This enables full Having developed Neptune, STL decided to take the motion compensation and station keeping accuracy. concept further. Why not a multi-axis articulated arm with
The company has developed a full-scale prototype, ?rst more intelligence, so that USVs could do more, such as tested onshore in 2017, both on a six degree of freedom equipment transfers, survey and inspection or launch and ship-motion simulator STL has and on land at STL’s re- recovery operations, from a moving object, i.e. a ship or
USV, to another moving object?
This is the synchronous stabilisation the company has been working on, or its Autonomous Synchronised Stabi- lised Platform (ASSP), that’s had European Regional Devel- opment Fund through the Marine-I programme in Corn- wall, where the company has another base. It adds machine vision to synchronise the payload motion with the moving target, so that, whatever motion the articulated arm is expe- riencing, the end of the arm has no residual motion with re- gard to the moving (?oating) object it’s synchronising with.
This could be used from ships for launch and recovery of ROVs and AUVs, says Andreas. Using a remote sens- ing system (RSS), developed by STL, and machine vision to detect robots in the water, the arm, from a host vessel, could be used to pick them out of the water, tho this would need a latching system added to the vehicles, he says.
A critical part of this system is a “Remote Sensing Sys- tem” (RSS), which STL had further Marine-I funding to develop. The RSS adds machine vision to the robotic con- trol system, enabling the movement of objects of interest to be tracked relative to a known datum. This is fed into the control system so the arm can synchronise with the object, such as an AUV, ROV, another vessel or a ?oating wind turbine, says STL.
The system was initially tested in 2020 using a ship- motion simulator and a moving target test rig, and since then there’s been a demonstration at the University of
Plymouth’s COAST Laboratory, which has in-water test- ing enabling physical model testing with combined waves, currents and wind. This involved a research prototype with a three-part articulated arm. It was limited to a 100kg pay- load, which would support deployment of a Falcon ROV or Gavia AUV, says Andreas. “But it would be applied to any robotic crane arm,” says Andreas. “It could allow ship- to-ship transfer. The geometry can be adapted to any ap- plication and heavy objects.” I.e. the technology can also be applied to a bigger system such as Neptune, says STL.
There’s still work to be done. The machine vision for remote sensing will need to be at a point where adequate robustness and reliability offshore is demonstrated.