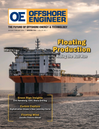
Page 53: of Offshore Engineer Magazine (Jan/Feb 2024)
Read this page in Pdf, Flash or Html5 edition of Jan/Feb 2024 Offshore Engineer Magazine
TECHNOLOGY ROVs
Image courtesy Copenhagen Subsea Image courtesy SMD enhanced workability or rock installation operations. The camera system. By integrating a 3D camera from Danish vehicle has an expansive on-board survey equipment suite UVision, we have unlocked a new level of subsea explo- developed for optimal positioning and operations manage- ration and inspection capabilities. With this cutting-edge ment, as well as for prime ability to monitor the environ- technology, the Gorilla ROV now has the ability to cap- ment and conduct pre- and post-surveys with Seatools’ ture highly accurate and detailed 3D scans of underwater specially developed multicore processing technology. environments. The 3D camera, mounted on the Gorilla,
Some companies have recognized the strong potential enables the creation of precise 3D models, providing in- for autonomy optimization in the recent advancements valuable insights for various applications. The 3D camera in AI technology, and this includes underwater robotics delivers exceptional image quality and resolution. Its ad- company QYSea Technology and their newly modular, vanced scanning capabilities allow for rapid data acquisi-
AI-powered advanced imaging and observational marine tion and precise measurements, ensuring accuracy in sub- robot, the FIFISH E-GO. The E-GO offers a range of ad- sea mapping and inspection tasks. With the Gorilla ROV vanced capabilities not often seen in the subsea tech mar- and its integrated 3D camera, subsea operators can now ket. With a detachable motor, lighting, camera, and bat- visualize underwater structures, assess damages, and plan tery, module replacements can easily and quickly restore interventions with greater precision than ever before.
operability. This feature also allows for extensive expan- Seatools completed Factory Acceptance Tests (FAT) for sion and customization of components. The E-GO has a Fall Pipe ROV developed for DEME, to be deployed on integrated AI into almost all operational aspects of their DEME's upcoming subsea rock installation vessel Yellow- vehicle. With AI Vision Lock, it has high-level adaptive stone, scheduled to join the feet in the frst half of 2024.
stabilization and can lock onto target objects with ease. Its The new Fall Pipe ROV introduces several unique features, plankton fltering algorithm is also AI bolstered, automati- including the integrated rotator, allowing for the offsetting of cally optimizing visuals, monitoring tasks across aquacul- the ROV's heading relative to the vessel heading. This helps ture, search and rescue, hull check-ups and more, and even to ensure an optimal vessel heading, enhancing the work- its laser scaling and measurement systems use AI automa- ability level of rock installation operations while saving sig- tion for increased accuracy and the ability to identify dam- nifcant power compared to conventional Fall Pipe ROVs.
age in underwater structures. The FIFISH E-Go is QYSea’s Another feature of the ROV is its expansive on-board most powerful professional-class underwater robot and is survey equipment suite, employed for precise ROV posi- now available across all QYSea platforms. tioning, monitoring operations and the environment, as
Latest innovation from Copenhagen Subsea is the en- well as conducting comprehensive pre- and post-surveys. hanced Gorilla ROV, now equipped with an advanced 3D To handle the vast amounts of data and complex control january/february 2024 OFFSHORE ENGINEER 53