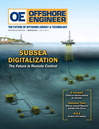
Page 49: of Offshore Engineer Magazine (Sep/Oct 2024)
Read this page in Pdf, Flash or Html5 edition of Sep/Oct 2024 Offshore Engineer Magazine
e recently visited with Fabian Hippe, Ma- rine Foundations Sales Director, Acteon, for a discussion on the new pile driving
W unit and the markets it will serve. Hippe, based just north of Hamburg, is well-suited to discuss the company and the market evolution, as he joined Menck in 2006 and for a ?ve-year stretch to 2021 served as its managing director.
“We are approaching the limit that mankind can build right now,” said Hippe, “as with the 6000 we have maxi- mized the weight of the ram that we can build.”
Though the Menck hammers were originally designed for [and still used in] the offshore oil and gas market, the
MHU 6000W is designed to meet the growing demands of the offshore renewable sector, opening up new possi- bilities for offshore wind projects by handling larger and heavier piles in increasingly challenging environments.
“Fifteen [or so] years ago we were talking about 2-4 MW turbines; today we’re installing 15-16 MW turbines, now we’re talking about 25 MW turbines. This is a massive step changes in technology,” said Hippe.
Everything about the offshore renewables market is big, and while there are starts and stops in some regions, Menck and Hippe are eying massive market growth for units of this size starting in 2028. Hippe said that today Menck has powered engine to drive a pile, said Hippe.
committed to the forgings for the new MHU 6000W, and To put the amount of power being laid down by its ham- the plan is to have them built and available for use by the mers in perspective, Fabian Hippe said the smallest unit in start of 2027 – aiming for 2027 to have it available. its arsenal today – a 100KJ, double impact hydraulic ham-
To put the growth of renewables in perspective, Hippe mer – delivers a force analogous to a Porsche crashing into said that ?ve years ago, offshore oil and gas accounted for a wall at about 28 mph. The new hammer coming to mar- about 60% of Menck’s revenue, the other 40% to offshore ket in 2027 is a 6250KJ system, “which is the equivalent of renewable energy. Today that script is ?ipped, and while a Porsche hitting a wall at 190 mph!
the offshore oil and gas business has been stable, “there Key features of the hammer include a double-acting has been a tremendous growth in renewables,” and today hydraulic drive, closed-loop control, shock absorber car- about 75% of Menck’s revenues come from offshore re- tridges and comprehensive safety mechanisms. By driving newable energy with about a quarter from oil and gas. a larger hammer at a lower energy, the Wind Hammer also reduces machinery wear and tear and minimizes underwa-
THE TECH BEHIND THE HAMMER ter noise.
The Wind Hammer is engineered to drive larger piles While driving impact is critical to ef?cient build out of in tougher environments and install longer piles in deeper offshore wind farms, so too is doing the job with a mini- waters, to enable the deployment of a future generation of mization of noise as ‘noise pollution’ is increasingly a point monopiles with top diameters of up to nine meters. Deliv- of contention in the world’s waterways.
ering from 100 kJ to 6,250 kJ of energy to drive monopiles “We need to drive the pile, but we need to be quieter in with diameters up to 9 m and beyond, the Wind Hammer the water column to adhere to regulations,” said Hippe. provides unmatched power and ef?ciency. He said making the equipment larger has actually had a
When Menck was formed more than 156 years ago by positive effect on the noise emitted. “two guys who joined together to manufacture boilers,” “Oversizing the equipment has a positive impact on even in the ?rst year of business they developed a steam- noise, as you’re striking with a heavier weight at a lower september/october 2024 OFFSHORE ENGINEER 49