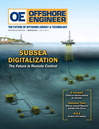
Page 53: of Offshore Engineer Magazine (Sep/Oct 2024)
Read this page in Pdf, Flash or Html5 edition of Sep/Oct 2024 Offshore Engineer Magazine
utonomous Underwater
Vehicles (AUV’s) have been introduced as ef?-
A cient tools for subsea pipe- line inspections. It has also been dem- onstrated that AUVs can be used to perform contactless and continuous electric ?eld measurements of the Ca- thodic Protection (CP) systems along pipelines. In this article we present a newly developed and commercialized sensor system for accurate and low noise electric ?eld measurements. We also present electric ?eld data along a pipeline section together with analysis
Figure 1. The AUV with the eight electrodes flush mounted and estimation of anode material con- with the hull.
sumption derived from continuous electric ?eld measurements.
This is important to achieve suf?ciently low noise during
Argeo Listen – measurement with low in?uence from the AUV platform
An electromagnetic receiver system itself. As a result, the sensor system provides highly reli-
The Argeo Listen electrode system consists of eight sil- able and calibrated electric ?eld measurements, with excel- ver/silvercloride (Ag/AgCl) electrodes mounted in ?ush lent signal-to-noise ratio (SNR) in CP measurements with with the hull of an AUV. Four electrodes are located in typical noise levels less than 0.005 µV/cm. In addition, the the aft and four in the front, ?gure 1. The mounting in motion stability of the AUV platform with high accuracy ?ush with the hull reduces turbulence noise and prevents navigation data enable electric ?eld measurements of suf- damages during AUV launch and recovery. Each electrode ?ciently low anode output electric currents for complete is connected through a cable inside the AUV to the ac- CP integrity evaluation along a pipeline.
quisition electronics mounted inside a pressure bottle. The The acquisition electronics controls the sampling, digi- bottle is placed inside the AUV in an area chosen with tization, and pre-processing of the EM-data before being the objective to minimize electromagnetic noise. The elec- merged with the navigation, heading, pitch, roll and envi- tronics bottle, cables and electrode housings and electrodes ronmental data as well as with magnetometer data. Auto- are depth-rated down to 6,000 m. matic quality control of the nav merged EM-data then en-
The eight electrodes are connected into eight pairs (chan- ables short turnaround time for evaluation of the CP status.
nels) where each channel measures an electric potential ?eld difference. The eight pairs are chosen to span the 3D space Efficient contactless CP-measurements redundantly and are used to construct the full 3D electric and analysis ?eld. The reason for this design con?guration is to achieve A working CP-system along a pipeline generates electric higher accuracy in the electric ?eld components compared currents in the seawater. In particular, electric current is to trying to measure them directly. The eight electrode pairs going out from each anode and returns into the structure also give redundancy which is useful if any or several of the at dedicated drain points or at places where the coating has electrodes should degrade during a dive. The redundancy been removed or damaged into bare metal. The CP-system also provides additional noise suppression. works as a galvanic element where the electric current in
The powering of the electronics from the onboard bat- the seawater generates an electric ?eld.
teries is designed to be independent on the charging levels An AUV equipped with the Argeo Listen electrode sen- of the batteries as well as independent on the power con- sor system continuously measures the 3D electric ?eld at sumption from other onboard payloads and instruments. a height of 5-10 m above the pipeline in a speed of 3-4 september/october 2024 OFFSHORE ENGINEER 53