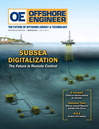
Page 64: of Offshore Engineer Magazine (Sep/Oct 2024)
Read this page in Pdf, Flash or Html5 edition of Sep/Oct 2024 Offshore Engineer Magazine
TECH NOTES NEW PRODUCTS, TECHNOLOGIES AND SYSTEMS
TORAY INDUSTRIES vessel is designed for all kinds of maintenance work on wind turbines up to 20MW, including replacement and
KNUD E HANSEN handling of nacelles weighing as much as 1,000t at a hub height of 175m, and managing blades up to 130m long.
Jack-Up Platform Enables All-Weather
This can be done while it is jacked up in 80m water depth.
Nacelle Maintenance
Knud E Hansen designed a “Jack-up on Jack-up” vessel
ABS Type Approval for In-Situ Carbon concept for offshore wind farm maintenance.
Fiber Composites Repair Technique
The four-legged jack-up vessel features a 15m wide Toray Industries became the ?rst in the world to obtain type working platform that can be jacked-up to the height of a approval from the American Bureau of Shipping (ABS) for its nacelle to provide a safe platform for maintenance work on vacuum-assisted resin transfer molding (VaRTM) process for the blades eliminating the need for hazardous rope access. in-situ ship repairs. The technique entails applying carbon ?-
With a telescopic weather cover ?tted on the platform, ber reinforced plastic (CFRP) to corroded areas with reduced work on the blades can be done in practically all weather thicknesses of ?oating production, storage and of?oading conditions, day or night, resulting in more working hours (FPSO) and ?oating storage and of?oading (FSO) systems. annually than with conventional maintenance vessels. ABS accounts for around half of FPSO and FSO certi?ca-
A large, air-conditioned workshop is located at the aft tions. This approval enables these certi?ed vessels to employ end of the work platform, and when the weather cover is the proprietary VaRTM process, reducing the time needed for deployed, a virtual factory hall is created around the blade, engineering reviews and veri?cations for ship repairs.
allowing all types of work to be performed on the blade, FPSO and FSO maintenance is normally offshore using minimizing the need to remove the blades and transport steel materials. The welding, or hot work, halts oil and gas them to shore for repair. production. Toray and MODEC, Inc., jointly developed the
Additionally, there is the possibility of inserting an X-Y VaRTM repair process in 2020. It entails applying Toray’s motion compensating system between the work platform TORAYCA carbon ?ber woven fabric, which offers excel- and the platform carriers so the “factory hall” can remain lent strength and elasticity, to the surfaces of existing steel geostationary. structures. The next step is to cover the fabric with a ?lm,
A “cherry picker” mounted on a hammer head at the plat- vacuum-seal, and inject epoxy resin that then cures to com- form’s opposite end provides the access to the nacelle. The plete repairs by bonding the CFRP to the steel structures.
main crane is ?tted on the elevating structure, allowing for Another advantage of this in-situ VaRTM process is the use of a conventional pedestal-mounted crane with a that it is easier than with regular steel-based techniques to boom that is approximately 30% shorter than that of a con- transport materials and equipment to locations and per- ventional wind turbine maintenance vessel, which should be form repairs faster and with fewer people and time. The able to reach the same height, providing a much better view procedure does not involve hot work, minimizing impacts of the blades and the nacelle from the crane driver’s cabin. on oil and gas production.
Measuring 154m in length and 64.4 m in breadth, the 64 OFFSHORE ENGINEER OEDIGITAL.COM