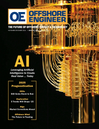
Page 37: of Offshore Engineer Magazine (Nov/Dec 2024)
Read this page in Pdf, Flash or Html5 edition of Nov/Dec 2024 Offshore Engineer Magazine
Image courtesy MAN ES
Head of Sales Upstream Industries, Holger Wörner sees an increasing demand for this small-footprint compressor technology. It is hermetically sealed, oil-free and employs seven-axes active magnetic bearings, so it dispenses with many components typically requiring maintenance in conventional topside compressor systems including gear- box, lubrication-oil system, instrumentation and valving.
Virtual sensors allow operators to validate measured data in real time, increasing operational effciency and ac- curacy while, leveraging machine learning capabilities, the system also continuously improves performance over time.
Digitalization is also helping optimize the faring pro- cess. With Baker Hughes’ emissions abatement technol- ogy, fare.IQ, bp is using critical information from its fare systems, including temperature, pressure, vent gas veloci- ties and gas composition, to help maximize combustion effciency and minimize emissions. Acting on real-time
MAN ENERGY SOLUTIONS IS SEEING INCREASED data from fare.IQ at 65 fares across seven regions, bp can
DEMAND FOR ITS HOFIM COMPRESSORS.
carry out early interventions to reduce emissions.
fare.IQ enables emissions reporting based on real-time measurement in compliance with the UN Environment tem. This totals just over 6 million standard cubic feet
Program’s Oil & Gas Methane Partnership (OGMP) 2.0 per day when the compressor dry gas seal system, fare level 4. Growing interest in measurement-based reporting network purge, and some provision for fugitive emissions is evident in the growth in OGMP membership which has are also accounted for. The result will be a reduction of about 50kT of CO2 per year or 1,250kT CO2 over the doubled to over 120 companies since its launch in 2020.
TotalEnergies has used AVEVA’s PI System to create a full operating life of the FPSO.
“We observe a dual trend,” says Le Touze. “A push to- digital platform that can perform emissions and energy effciency calculations in real time based on inputs such wards reducing emissions driven by international organi- as fuid composition, process design data and operating zations, national regulators, client policies, fnancial insti- parameters. It can now provide real-time calculations of tutions and SBM’s own initiatives, alongside a need for new technologies to emerge. Many technical solutions al- 85% of scope 1 GHG emissions across all of TotalEner- gies’ operated E&P assets. It is being used for purge gas ready exist that could signifcantly reduce emissions, with the primary one being amine-based carbon capture for optimization, to categorize faring sources, to detect pass- which SBM has developed a standard module based on ing valves and to detect process control anomalies.
our Fast4ward program. However, these solutions are not
Laurent Le Touze, SBM’s Product Development Direc- always selected by the oil companies due to a lack of CO2 tor, points to the importance of faring equipment opera- tion. “Amongst the key challenges to be overcome, there disposal options in the feld or because of insuffcient in- are preventing over-pressurization of the fare system and centives to justify the additional investments.”
The Agogo FPSO, designed with a full suite of carbon fare gas recovering compressor, preventing oxygen ingress in the gas treatment system and ensuring faring functions emission reduction technologies, will be the frst FPSO featuring carbon capture technology. Its construction as required, including fare tip ignition.”
Closed fares offer reducing emissions and without was contracted to Yinson Production by Azule Energy, visible fame or heat radiation, and the frst unit with a a 50/50 joint venture between bp and Eni. With an esti- mated reduction in carbon emissions of 27% compared closed fare that SBM will operate is the Almirante Ta- mandaré FPSO in Brazil from 2025. The closed fare gas to a conventional design, the FPSO also includes a closed fare system, hydrocarbon blanketing, combined cycle capacity is calculated based on all continuous very low- pressure gas streams from the produced water treatment technology, automated process controls and all electric drive systems.
and the triethylene glycol (TEG) gas regeneration sys- november/december 2024 OFFSHORE ENGINEER 37