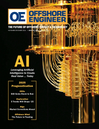
Page 43: of Offshore Engineer Magazine (Nov/Dec 2024)
Read this page in Pdf, Flash or Html5 edition of Nov/Dec 2024 Offshore Engineer Magazine
experience to redesign and increase the power range of its Marine Electrical Connectors (MECON) high volt- age AC wet mate connector to reduce the impact of cable failure. The company’s three-phase wet mate connectors consolidate three connections into a single housing, opti- mizing insulation fuid cleanliness while minimizing po- tential leak paths compared to the single-phase connec- tors used by others in the industry. These require three connections for every cable and therefore create three potential leak paths.
“If you look at other technologies, there are three in- dividual connections inside a connection frame that just looks like a single connector. The beneft of our system is that all three individual phase connections are really in a single mechanical connector,” says Mike Birch, Product
Manager for Offshore Power Systems at Baker Hughes.
The connectors are ROV fushable, meaning that they can be installed by a ROV that frst fushes the connector- collector interface with seawater to clear away any debris.
This is followed by fresh water fushing then ethanol be- fore the dielectric oil is injected. The oil initiates and iso- lates the electrical connection.
Baker Hughes has been scaling up their wet mate con-
SUBSEA REDESIGN UNDERWAY nectors from the original 12kV version, frst used in oil and gas in 1999, up to 36kV and now 66kV for foat- ing wind applications. The company is being assisted by energy majors potentially interested in the yet-to-be-de- ployed connectors. Their input has been invaluable, says
FOR FLOATING OFFSHORE WIND
Birch, as existing IEC standards only cover connectors up to 36kV and the industry needs a qualifcation matrix that will be broadly accepted.
The connectors interface to a subsea collector hub. Here he 66kV high voltage wet mate connector cur-
Baker Hughes has aimed at simplicity, at least for the frst rently undergoing technical qualifcation by Bak- generation of equipment, so the collector hub is essen- er Hughes weighs in at around one ton and has tially an oil-flled enclosure with wet connectors around over 40 liters of dielectric oil protecting copper the outside. “There are no moving parts within our ME- cable up to 1,200 square millimeters in diameter. CON Collector, there’s nothing smart inside the box, it
T
The connector is designed to sit on the seabed at the end simply collects power through multiple inputs and exports of a dynamic cable coming from foating wind turbines it through one output.” and connect it to a collector hub that ultimately delivers
As there is no defned switch gear at the collector, the the megawatts of energy it produces to a subsea substation Baker Hughes wet connect provides this functionality via and then to shore.
an internal disconnector which is operated via ROV and
There’s a lot that could go wrong. Cable failure is a high- is designed to isolate a cable using the switch in the con- cost problem for fxed offshore wind even though, like oil nector after the array is powered down. The transition to and gas applications, it involves static cabling. Dynamic having switches in the collector hub so the task could be cable failures are expected to be even more common when performed remotely and under electrical load may come in the foating wind industry takes off.
time, but for now Birch believes simplicity and lower costs
Baker Hughes has therefore leveraged its oil and gas are what the industry needs.
november/december 2024 OFFSHORE ENGINEER 43