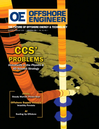
Page 15: of Offshore Engineer Magazine (Jan/Feb 2025)
Read this page in Pdf, Flash or Html5 edition of Jan/Feb 2025 Offshore Engineer Magazine
Image courtesy ABS
Petrobras, who are commissioning high-capacity FPSOs, exceeding 200,000 barrels per day.
Tremblay notes, “Conversions can’t accommodate FP-
SOs of this scale, as they’re larger than even the biggest ultra-large crude carriers (ULCCs). And with limited ship- yards capable of building them, costs are naturally higher.”
SBM Offshore’s Fast4Ward program is one example of maximizing ef?ciency, a program which builds FPSO hulls on spec, essentially helping to shorten delivery timelines, bringing new builds below the traditional 36–40 months to under 30 months.
Even with ef?ciency ?xes, the global supply chain re- mains a critical concern for FPSO construction. Tremblay
The cost of FPSOs emphasizes that while equipment delivery delays have sta- bilized, prices continue to rise. has soared. The P-78 FPSO “The cost of FPSOs has soared,” he said. “The P-78 was contracted at $2.5
FPSO was contracted at $2.5 billion, but just a few years later, P-84 and P-85 are each valued at $4.1 billion.” billion, but just a few years
One factor behind this cost escalation is vendor strategy, later, P-84 and P-85 are as they take a more measured approach to growth. Tremblay compares FPSO equipment manufacturers to offshore drill- each valued at $4.1 billion.” ers: “After years of ?nancial losses, they’re holding off on ex- panding capacity and instead capitalizing on high demand.”
Another factor in the cost equation is, of course, the shipyard.
With only a handful of shipyards capable of building FP- – MATT TREMBLAY,
SOs, the market remains constrained and China dominates,
VICE PRESIDENT, GLOBAL with four to ?ve active yards, while South Korea’s Hanwha
OFFSHORE AT ABS is aggressively competing for market share, leveraging geo- political concerns, speci?cally U.S./China relations.
Meanwhile, even the shipyards that dominate the FPSO tough, especially with FPSOs getting bigger,” says Trem- sector are actively weighing their options, as shipyards blay. “We need digital twins—fully integrated, real-time must weigh the size and particularly the length of FPSO asset models that allow operators, regulators, and class so- contracts against more pro?table alternatives like gas car- cieties to collaborate on maintenance plans.” riers. “FPSOs take a lot of steel; they’re big; they take up Remote inspection tools like drones, cameras, and Li- a ton of space. I can probably build three, maybe four DAR are advancing but remain limited by the need for gas carriers per square meter of dry dock space versus one physical cleaning. “You can’t detect bottom pitting corro-
FPSO; so I’m making more money building gas carriers sion if the tank is covered in sludge,” Tremblay explains. than I am building FPSOs,” observed Tremblay. “That’s why the new double-bottom FPSO designs will be a game-changer,” as they simplify tank cleaning, reduce
FPSO MAINTENANCE & THE DIGITAL SHIFT manpower and improving inspection ef?ciency.
While designing and building modern FPSOs present At the same time, FPSO designs are also evolving to their own challenges, once built and operational a growing align with sustainability goals, with companies like Yin- challenge for FPSO operators is maintaining these larger, son and Petrobras pioneering technologies such as onboard more technically complex vessels. Traditional calendar- carbon capture and FPSO electri?cation.
based maintenance cycles are giving way to vessel-speci?c, “Petrobras’ new FPSOs will operate like electric cars— condition-based maintenance strategies, supported by dig- using large natural gas turbogenerators to power electric ital tools and remote inspection technologies. motors instead of diesel engines. This reduces CO2 emis- “Inspecting every tank in a ?ve-year cycle is logistically sions by approximately 20%,” says Tremblay.
january/february 2025 OFFSHORE ENGINEER 15