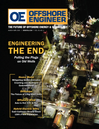
Page 53: of Offshore Engineer Magazine (Mar/Apr 2025)
Read this page in Pdf, Flash or Html5 edition of Mar/Apr 2025 Offshore Engineer Magazine
Periodic sampling and testing are also crucial in identifying issues early in the field." – Paula Lepore,
Chief Engineer at Parker
Hannifin’s Instrumentation
Products Division,
Parker Hannifin offshore structures," Godha explained. "These phenomena ners, using stress relief annealing, and ensuring proper can initiate cracks earlier than expected and cause rapid welding, is essential.
propagation, compromising structural integrity and re- Cathodic protection, a technique to reduce metal quiring costly repairs." corrosion electrochemically, is also vital. Keeping wa- ter from stagnating and allowing proper drainage can prevent localized corrosion. Having redundant systems
Monitoring and Testing Techniques in place as a safeguard against unexpected failures is
Detecting SCC and HE early is essential for prevent- ing long-term damage. While visual inspection is the most equally important.
straightforward method, it is often insuffcient, particular-
Real-World Challenges and Solutions ly for subsea structures or hard-to-reach areas. Advanced non-destructive testing (NDT) methods, such as ultrason- One practical example shared by Godha involved chem- ic testing, magnetic particle inspection, and dye penetrant ical injection skids used in the oil and gas industry, where testing, are more effective. Additionally, electrochemical components are exposed to extreme pressures (up to 15,000 techniques can assess material susceptibility to corrosion, PSI) and corrosive environments. Traditionally made from while standardized chemical testing, like ASTM G123 and coiled stainless steel, these components are prone to SCC
G38, help evaluate different alloy grades. under high stress and chloride-rich conditions. Such sce- "A combination of monitoring and testing methods of- narios illustrate the importance of understanding material ten provides the most comprehensive assessment," Lepore behavior under real-world conditions, beyond lab testing.
noted. "Periodic sampling and testing are also crucial in In the power generation sector, highly stressed alloys ex- identifying issues early in the feld." posed to atomic hydrogen can suffer rapid embrittlement, leading to catastrophic failures. Managing these risks re- quires a nuanced understanding of both material proper-
Proactive Mitigation Strategies
When it comes to mitigating the effects of SCC and ties and environmental factors.
HE, prevention from the outset is paramount. This
The Future of Mitigation: means selecting the right materials during the design phase—preferably alloys that can withstand the harshest
Innovations on the Horizon environments. Additionally, minimizing stress through
Looking ahead, advanced material development is lead- appropriate design practices, such as avoiding sharp cor- ing the charge in combating SCC and HE. High-perfor- march/april 2025 OFFSHORE ENGINEER 53