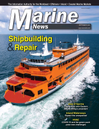
Interview: Joey D’Isernia, President, Eastern Shipbuilding
Eastern Shipbuilding Group is one of America’s leading shipbuilders. Perhaps best known for its history building tugs, towboats and offshore supply vessels, the company is today finding success in other markets, with notable build projects underway for the U.S. Coast Guard, Staten Island Ferry and dredging contractor Weeks Marine. Eastern’s president Joey D’Isernia weighs in on the yard’s current workload, market drivers and the challenges overcome and on the horizon.
Where do you see the best opportunities for Eastern Shipbuilding Group today?
We see a lot of opportunity in the defense sector, which is why we have dedicated our Nelson St. Shipyard to the U.S. Coast Guard Offshore Patrol Cutter (OPC) program. We are committed to delivering high quality, innovative, and efficient OPCs to the men and women of the Coast Guard on or ahead of schedule. We are competing for Stage II of the program, which would be ships five through 15 over the next 15 years.
We also expect to continue to see opportunities in the commercial dredge and offshore wind markets. We were recently awarded a second hopper dredge from Weeks Marine. ESG’s business is based on superb customer relations and a high performing workforce with proven results. We are committed to continuing our tradition of service to our commercial customers worldwide, and with our newly opened Port Saint Joe facility, we are also committed to becoming a trusted partner for vessel sustainment for both commercial and government customers.
In addition, we see growth in the energy and transportation sectors where energy development and the rise in consumer goods fuel growth. As fleets age, the repair market is trending positively for the foreseeable future, which was the impetus for our new Port St. Joe facility and drydock project. We also saw our new dry dock as an opportunity to reduce costs and potential schedule disruption for our new construction projects since many of the new build projects require docking prior to delivery.
Will you please give a status update for the newbuild projects Eastern currently has underway and lined up?
The Coast Guard awarded detail design for the Offshore Patrol Cutter to Eastern on September 15, 2016. Long Lead Time Materials (LLTM) was awarded in September 2017. Construction began in fiscal year 2018. Delivery of the lead OPC is planned for fiscal year 2022.The contract includes options for production of up to four vessels. To date, Eastern has earned the award of construction for OPC one through three and the LLTM contracts for OPC one through four. We have earned those contracts by executing for our USCG customer on time and on budget. The USCG plans to award construction of the fourth cutter in spring of 2022.
ESG recently completed Builder’s Trials and Contract Trials for the first of three NYCDOT Staten Island Ollis Class ferries and has received ABS class certificates as well as the USCG Certificate of Inspection. The vessel was recently towed to New York Harbor and is preparing its final acceptance trials, which is essentially duplicating the trials it has already completed at our facilities in Panama City, Fla. Construction of the second and third ferries are continuing on schedule, and we look forward to delivering them to our customer and its ridership.
We are honored that Weeks Marine decided to return to Eastern Shipbuilding for another hopper dredge. Our experience dealing with them on the Magdalen was a very good one, and together we delivered a state-of-the-art hopper dredge to the Jones Act Fleet. We continue to make great progress on their second vessel—a 8,550-cubic-yard twin screw trailing suction hopper dredge—and we remain on schedule and on budget despite building the vessel in the midst of the COVID-19 pandemic. This is the third hopper dredge to be built by ESG, and it cements our position as a proven builder of large, highly sophisticated hopper dredges.
Staten Island Ferry’s first Ollis Class vessel on sea trials (Photo: Eastern Shipbuilding Group)
Earlier, you mentioned the new facility in Port St. Joe. Will you please tell us a bit more about that yard and how will it impact the company overall?
We opened our third facility in Port St. Joe, Fla., in nearby Gulf County, where we are currently outfitting and testing the Staten Island Ferries. With the addition of the PSJ facility, we have expanded our capacity and are thus more responsive to meeting the dynamic needs of our customers.
This facility encompasses 40 acres and 1,000 feet of deepwater bulkhead with unrestricted access to the Gulf of Mexico test and trials grounds only a few short miles away. This facility is dedicated to final outfitting and testing of commercial new construction vessels as well as topside repairs. We have embarked on a $50 million, 15,000 ton drydock project at this facility in order to provide full vessel sustainment services. This dry-dock has been specifically designed to be able to service government ships as well as commercial ships and can haul deep draft vessels as well. We have just completed a $6 million infrastructure improvement project at our Port Saint Joe facility to allow for vessel outfitting to commence. Once our dry-dock is in operation, we will become a full-service vessel sustainment facility that can accommodate both commercial and government customers. We have grown our facilities organically and this has ensured our company culture of integrity, safety and quality are alive and well. Additionally, this location enables us to tap into another labor market to support our projects.
How else is Eastern investing today to ensure future success?
We have invested in equipment, processes and procedures to minimize the impacts to the environment where we live, work and play. All our facilities are ISO 14001 compliant. This certification means that we adhere to processes and procedures designed specifically to minimize our overall environmental footprint whether it is carbon emissions, keeping our waterways clean or reducing waste through recycling initiatives to name a few. We have been ISO 14001 certified since 2012 and plan to continue this tradition moving forward. The industry is rapidly moving into zero emissions and reduced footprint across the board, and we are proud to be leaders in that effort.
Additionally, we have built and are currently operating a technologically advanced telecommunications testing facility called a Production Facility (PF) This asset ensures the C5ISR capabilities are seamlessly integrated into our government vessels and that integration risk is drastically reduced through full up-front testing prior to installation on the ship.
Last but not least, we are in the process of investing approximately $45 million into infrastructure improvements across all of our facilities in an effort to meet the current and future needs of our customers and to maximize efficiency.
How has the COVID-19 pandemic materially impacted your company to date? How do you expect business will be affected going forward?
COVID-19 has affected everyone in this nation and the world, and ESG is no different. We had to quickly adapt our way of business to deal with the new reality, but first and foremost we looked after our employees and our community. We have been and are currently following health and safety protocols as recommended by the CDC to keep our employees and families safe. We remained operational with protocols in place, such as temperature checks, masking, social distancing, hygiene, testing, and quarantines. We had vaccination clinics onsite at our facilities to make vaccines readily available to our employees who chose to become vaccinated. We hope we can all return to a more normalized environment soon. That being said, we are not letting our guard down and doing all we can to combat the virus. Even though COVID-19 made it much more difficult to build ships, we made commitments to our customers, commitments that we have kept.
Many shipyards have trouble finding, hiring and retaining talent. Do you find this to be a challenge today, and what is Eastern doing to ensure it has the workforce it needs?
We have been operational for over forty years, and we expect to be for decades to come thanks to our dedicated team. The pipeline of work that we’ve captured and plan to capture both commercially and through the OPC program offers skilled workers a rewarding long-term career. Because of this, we have been able to recruit talent that is locally trained and attract workers from outside our area. We’ve recently enhanced our benefits package to attract and retain workers and continuously look at ways to grow our pool of workers, which is why the Port St. Joe facility is so strategically placed. We have also partnered with many area educational institutions from high schools to colleges in order to stand up training programs tailored specifically to a shipyard employees’ training needs. Attracting, training and retaining shipbuilders is a challenge for all American shipbuilders, and we must place emphasis on training the next generation of craftsmen.
Eastern has dedicated its Nelson St. Shipyard to the U.S. Coast Guard Offshore Patrol Cutter program (Photo: Eastern Shipbuilding Group)
Eastern was hit hard by Hurricane Michael in 2018. Please describe the storm’s full impact to business and Eastern’s build schedule. And what did the road to recovery look like?
Much like the rest of Bay County, ESG facilities were virtually unrecognizable after the storm, nearly every structure was damaged or destroyed. We had a monumental challenge ahead of us. Immediately following the storm, we set out on an aggressive initiative to locate all our employees and help get them back on the job as soon as practical after they took necessary time to secure the safety and security of their family and home. Together with our network of friends, partners and customers in the maritime community, ESG organized daily distribution of meals and goods to employees in need. Additionally, ESG created an interest free deferred payback loan program for those employees in need and successfully organized a Go Fund Me account, raising nearly $250,000 to help those employees hardest hit by the storm. ESG also knew temporary housing was going to be a necessity in the short term and immediately built a small community located on greenfield space near our facilities for those employees with temporary housing needs. In two weeks after the Hurricane we were able to resume operations with at least 80% of our workforce.
We have rebuilt our facilities thanks to the hard work and determination of each ESG employee, as well as the support of our families, friends, neighbors, vendors, customers, and federal, state, and local partners. We are still building, expanding our shipyards and capabilities every day. We could not be prouder of our employees and how far we have come since the Hurricane.
How would you describe your management philosophy?
We always keep our promises, and our quality is unmatched. This is due to our strong company culture combined with our skilled and committed workforce. We have a reputation for producing the highest quality marine vessels in the industry, delivered on time and on budget. On several occasions, we have been called upon to take over and complete projects that have failed at other shipyards. We have also built a reputation of trust. We keep our word and deliver results because that is the right thing to do. Even if it comes at an economic cost to our business, our customers can count on us to we get the job done.
Our company is a family business that has always made it a point to give back to the community. Our community is our home, and we want to do our part to help it thrive. We have been very involved in local charities designed to help children affected by domestic abuse, have partnered with our school district to bring training programs to our area, and are involved in volunteer work with our local hospitals.
We keep values like these at the forefront as we manage our business, and they flow down through our management chain all the way to the deck plates. This is why our employees won’t leave a job until they are satisfied it is done right.
Eastern is currently building the new Offshore Patrol Cutters for the U.S. Coast Guard. (Image: Eastern Shipbuilding Group)
While I know your portfolio of work is broad, please provide an in-depth look at one recent project that you consider to be particularly challenging, gratifying or otherwise indicative of the work that you do.
Eastern Shipbuilding is proud to be delivering for the USCG the Heritage Class Offshore Patrol Cutters. We celebrated the keel authentication of the first vessel, USCGC Argus, with the Commandant and Coast Guard leadership in 2020. Argus will be ready for delivery in 2022. Hulls two (keel laying completed May 2021) and three are currently under contract as well demonstrating ESG’s ability to execute multiple concurrent hull construction projects. This multibillion-dollar acquisition is the Department of Homeland Security and USCG’s highest investment priority. The OPCs represents the backbone of the Coast Guard’s cutter fleet, bridging the capabilities of the 418-foot national security cutters, which patrol the open ocean, and the 154-foot fast response cutters, which serve closer to shore. The OPCs will conduct missions including law enforcement, drug and migrant interdiction, search and rescue and other homeland security and defense operations. Each OPC will be capable of deploying independently or as part of task groups and serving as a mobile command and control platform for surge operations such as hurricane response, mass migration incidents and other events. The cutters will also support Arctic objectives by helping regulate and protect emerging commerce and energy exploration in Alaska.
We are executing for the USCG by delivering unparalleled quality of construction while at the same time utilizing proven, DCMA certified business management systems specifically tailored to this government project. I am confident we will continue building forward momentum as we partner each day with the USCG to deliver excellence in government shipbuilding.
ESG has demonstrated incredible resilience and ability in producing these state-of-the-art national security vessels through major setbacks brought on by Hurricane Michael and COVID-19.
Eastern Shipbuilding is the best and lowest risk choice for quickly and reliably introducing OPCs of demonstrated high quality into the active fleet because we provide a uniquely mature OPC design and 3D model that meets OPC specifications, a proven, fully documented production approach and ample, modern facilities dedicated to, and currently executing, OPC production.
We are proud to work with the best engineers and innovators in the industry. We have contracted more than 200 vendors in 34 states and many of them are minority-owned and small businesses. We partner with companies who share our philosophy of quality and results and when we find those like-minded suppliers, we remain loyal to them.
Read Interview: Joey D’Isernia, President, Eastern Shipbuilding in Pdf, Flash or Html5 edition of September 2021 Marine News
Other stories from September 2021 issue
Content
- Ferries V2.0. Post COVID Opportunities page: 12
- Interview: Joey D’Isernia, President, Eastern Shipbuilding page: 14
- Prefabrication of Federal Shipbuilding Project Funding page: 20
- The Case for Stock Boats page: 22
- Expect the Unexpected on the Inland Waterways page: 24
- HVAC: Three Challenges to Challenge Engineers page: 30
- Tech File: Automated Welding Solutions page: 36