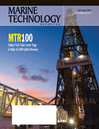
Page 39: of Marine Technology Magazine (July 2010)
MTR100 Edition
Read this page in Pdf, Flash or Html5 edition of July 2010 Marine Technology Magazine
Boeing
Anaheim, CA
Tel: (714) 762-5838 • www.boeing.com
Boeing Chairman, President and CEO: Jim McNerney
Director, Maritime ISR Systems: Tom Jones
Facilities: Maritime ISR Systems occupies two buildings that include engineering and support offices, high capacity computer networks, and test, integration and manufacturing areas including high-bay test areas with 10- and 40-ton cranes.
Square Footage: 200,000 sq. ft. of engineering, test, integration and production space, of which 40,000 sq. ft. is dedicated to undersea programs.
Testing Capabilities: In addition to the above, Maritime ISR Systems’ footprint includes certified bat- tery recharging facilities, a 10,000 psi test chamber, and a 120’L x 90’W x 33’D test pool which is enclosed to handle various levels of security.
Employees: 140
Formerly part of Rockwell International, Maritime ISR
Systems has produced more than 36 undersea systems during its 40-year history. The company specializes in sub- marine systems integration, autonomous software, com- plex low power systems design, launch and recovery design, mission/sortie planning, open systems command and control, real-time/faster-than-real-time simulation, undersea systems networking, and acoustic processing.
A sampling of early programs in the 1960s and 1970s includes the Dolphin UUV, Powered Underwater
Research Vehicle (PURV) and Beaver. A few of their other milestone programs were MK40, Unmanned Free
Swimming Submersible (UFSS), and the initial Remote
Mine Operational Prototype (RMOP). In parallel with the vehicle design, Boeing has invested in development of high-level, fault-tolerant autonomous software. Current field-tested systems include the Navy’s AN/BLQ-11 (mine survey UUV) and the Echo Ranger LDUUV (recently transitioned from commercial surveying to a DoD devel- opment testbed). Maritime ISR Systems’ acoustic pro- cessing heritage is also impressive with more than 30 years of providing hardware, software and interface design for airborne, shore-based and shipboard acoustic processing.
Current programs include the analyzer subunit (ASU) of the USQ-78B for the P-3 Orion and the acoustic process- ing suite for the P-8A Poseidon. Combined, these two programs provide sonobuoy acoustic processing for all US
Navy fixed-wing ASW aircraft.
The AN/BLQ-11 autonomous Unmanned Undersea
Vehicle (UUV), formerly called the Long-term Mine
Reconnaissance System, was designed for covert mine countermeasure capability. It remains the US Navy’s only submarine-qualified 21-in. heavyweight vehicle. The autonomous UUV carries multiple sonar and navigation systems and control software for the mine reconnaissance mission. The BLQ-11 system is a temporary alteration (TEMPALT) and the vehicles and shipboard deployed equipment are all handled and loaded like a torpedo. In
January 2006, several UUV “firsts” were accomplished, including full impulse torpedo tube launch, repetitive helo recovery, following an SSN through 180-degree turns, and successful docking to an SSN while underway. During two sequential attempts in October 2007 tests, each
AN/BLQ-11 UUV was successfully launched from a U.S.
Navy attack submarine, then returned to the vessel where the system’s robotic arm retrieved the vehicle back into the submarine. AN/BLQ-11’s sister vehicle is Echo Ranger, an autonomous large displacement unmanned undersea vehicle (LDUUV). This COTS-designed system with a maximum operating depth of 3000 meters has logged more than 2000 miles in tests and surveys (up to 28 hours) and could be configured for 30-day missions. www.seadiscovery.com Marine Technology Reporter 39
MTR 100