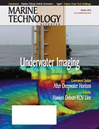
Page 30: of Marine Technology Magazine (October 2010)
Ocean Engineering & Design
Read this page in Pdf, Flash or Html5 edition of October 2010 Marine Technology Magazine
and digital enhancement are only capable of improving imagery within a few meters. Imaging sonars can detect and classify objects based on shape at a greater range but cannot show component detail clearly at greater distances or the positions of multiple structures in what may be a complex subsea field layout with infrastructure spread out over several kilometers. Augmented Reality (AR) Viewers offer the ability to rapidly fly through and view field assets with perfect visibility either from the perspective of an onboard ROV camera or from any stand-off distance.
This improved situational awareness and ability to instantly jump to and view individual asset components enables faster field familiarization and saves considerable time during survey planning and when reviewing results.
Additionally, being able to zoom in and rotate around structures to see more component detail and consider dif- ferent methods of access enables Inspection Engineers to plan survey inspections using ROVs well in advance.
The field view is built using accurate models of struc- tural members and components. Owners often have their own nodal identification hierarchy which can be used for easier recognition and tracking within the AR viewer dur- ing inspection. For greater efficiency and return on invest- ment, these models can be re-used at each stage of the inspection process from definition of a task based workscope generation, through the offshore inspection process and on to the subsequent analysis and review in client offices.
The virtual field is laid out based on survey positions of assets. Significant operational downtime is saved by plan- ning a course that stays clear of obstructions/risk areas and by working out how to approach inspection targets in a safe and efficient way. This technology is moving fast and it is now possible to track live positions within this virtu- al world. By attaching position, pitch, roll and heading sensor feeds to one or more ROVs/vessel models it is pos- sible to update the 3D model in real-time showing track data, camera views and multi-beam coverage of the seabed. This is leading to a real-time network distributed view of all field operations within the 3D Field Model. A wider audience benefits from being able to view live oper- ations within the field: pilots, crane operators, operations supervisors/superintendents, owner/operator representa- tives and increasingly onshore teams who may access the system via a SatCom link. Direct, real-time ROV position feedback through an AR Viewer can also be used along- side existing vision-based systems to aid pilot navigation.
Used as part of an Integrity Management (IM) solution,
AR Viewers offer front-end access to different client struc- tural datasets in a single 3D simulation of the field.
Datasets are mapped to specific structural component IDs so that users can see and extract catalogues of data from current or previous inspection campaigns for comparison, interpretation and risk management.
Inspection Workscope Visualisation
Inspection Engineers need to take a lot of factors into consideration when deciding how to implement an inspection strategy. Different types of asset have different risk factors so inspections need to be tailored to the asset.
Risk-based techniques are used to decide when to inspect and what types of failure to target. Inspection Engineers use their experience together with knowledge of the age of the asset, its original expected design life, its inspection and repair history, and its operational environmental to define a work scope of inspection targets. The ability to easily visualize, review, select and sequence different com- ponents for inspection based on ready access to this kind of target information makes inspections quicker to plan, track, audit and report on.
However, Inspection Engineers get what they inspect rather than what they necessarily expect. So what happens when unusually aggressive deterioration is observed or the
Inspection Engineer finds anomalies in areas where it was not expected? After anomalies are logged and classified more evidence needs to be collected to see how wide- spread the effects are, and to find out if other components of the same type are affected to a similar extent. Therefore,
Inspection Engineers need online tools to record what is found, keep track of what has and has not been inspected and be able to modify the scope of work as required to undertake more detailed inspections or to survey a larger sample of targets.
To get a comprehensive picture, Inspection Engineers need to tie all inspection data together. This is a complex problem that requires synchronisation between the online data acquisition system, offline review system and compo- nent model datasets. It involves linking recorded video, survey positioning, sensor measurements and condition observations with members and components and then providing access to histories of previous inspections.
Referential documents such as standards, classification rules, company rules and procedures for inspection also need to be readily accessible. Having all this data in one place and accessible using a single user interface makes it much easier and faster to conduct condition analysis and generate inspection reports.
Improving workscope visualization and task tracking 30 MTR October 2010