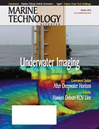
Page 42: of Marine Technology Magazine (October 2010)
Ocean Engineering & Design
Read this page in Pdf, Flash or Html5 edition of October 2010 Marine Technology Magazine
MacArtney’s new American
Petroleum Institute (API) approved connector helps ensure Hydril’s new blow out preventer system will func- tion if needed. Automatic BOP sys- tems constantly monitor the well and are designed to be fail-safe devices.
Not only must they be periodically inspected and tested, the American
Petroleum Institute sets standards that are clear about the types of risks against which such equipment must be protected. New designs are rigor- ously tested and certified and each element must meet stringent require- ments before being API certified.
The size of the preventers and the depth at which they are deployed makes them impractical to bring to the surface often for testing. And as drilling sites are in increasingly deep- er waters, BOPs have become more advanced. They must withstand the increased pressures at depth and they must also be reliable enough to per- mit increased intervals between tests or servicing. Systems and equipment on the BOP can be submerged for up to a year between servicing and must therefore be resilient to the harsh underwater environment.
When Hydril was designing its new
BOP Control System, the company needed a complete infrastructure package that met the strict standards for testing and reliability stipulated by the American Petroleum Institute.
The connector system within the complete unit needed be able to with- stand submersion for extended peri- ods and accommodate several failure modes stipulated in the American
Petroleum Institute Pressure Controls guidelines. These stipulations includ- ed the requirement for the umbilical or termination assembly to function even when fully flooded with seawa- ter and continue to operate for an extended period without conductor failure. A comprehensive design, build, test and deploy, program was implemented to fulfil the require- ments of outfitting Hydril with three rig packages and just as many spares and test units. The brief was to fulfil
American Petroleum Institute stan- dards 16D for testing when assem- bled and the harder to attain 17E for functionality when flooded. Ensuring that connectors for the infrastructure system would function even if the cable was flooded required the com- bination of several design features. A boot was fitted behind the connector to ensure that any water entering the cable cannot penetrate to the connec- tor and the connector will continue to work for its intended lifespan even with water flooding in the cable right up to the boot. For 17E standard cer- tification, the cable is as important as the connector. The cable was selected for its ability to withstand wear underwater. The conductors inside the cable are also protected to prevent water ingress shorting the connec- tions. Critical to the design was ensuring that the connector could be tested for integrity once assembled.
MacArtney designed and integrated double test ports on the API connec- tor itself to allow pressure testing of both sections after mating and before the connection is lowered into the water. Each system needed to be fail- proof on delivery and was tested at various stages of production and completion. Every element in the cable was tested individually before construction to ensure that they were entirely intact and fully functional.
The cable, and then the connector and cable were pressure tested before completion. The entire cable and connector unit were ultimately pres- sure tested prior to inclusion in the infrastructure package. The system has evolved over several years into a comprehensive high reliability power and communications infrastructure package for semi-submersible drilling rigs in operation around the world.
The complete infrastructure package includes fibre optic media converter, multiplexer, MUX cable, slip ring, subsea stress termination, subsea
FITA terminations, all subsea harness cable and POD connections.
The birth of a new range
The connectors have achieved a type certification that controls vari- ous design parameters and governs the production, testing procedures and metrics. MacArtney can vary the connector form factor of these con- nectors provided they fall under the type certification requirements and now offers a range of API (American
Petroleum Institute) approved con- nectors.
Email sf@ macartney.com, or www.macartney.com products 42 MTR October 2010
The Strongest Link